We’ve seen the advent of printed homes, but how feasible would it be to scale that 3D-printing technology to create the bulk of our built environment in the future? Would it be possible to automate a 3D printer to construct hundreds, or even thousands, of homes? 3D-printed construction suggests great promise with the potential to reduce costs and accelerate build times. But to get there will require a revolution in architectural and engineering design processes.
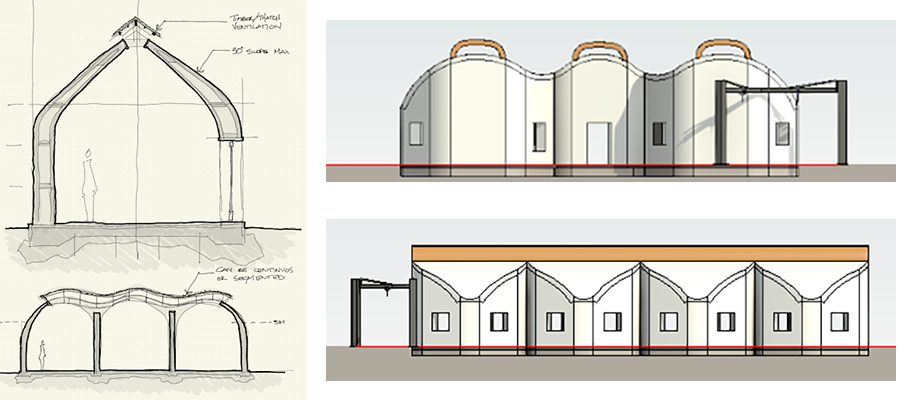
From architectural draft to BIM of a 3D-printable building. Images: Charles Newman and Emily K. Schwartz
In the modern era of architectural design, the architect is both guided by, and bound by, the tools of architectural representation. One of the software packages that increasingly shapes the design workflow of an architectural design office is Revit, Autodesk’s Building Information Modeling (BIM) software. The platform, already widely adopted across the industry, incorporates site constraints, material data, and architectural standards into prescribed properties for foundations, framing, drywall, siding, and so on. While this platform has proven to be extremely useful in coordinating complex projects, it is still bound by the assumptions of conventional construction processes that limit its use in the design of a mechanized, additive construction project.
The only appropriate workflow from Revit to a 3D Printer first requires the designer to manually remove all extraneous elements, distilling the model to only those elements to be printed. Revit does not have the capability to export a file as a mesh; nor does it have a “slicing” capability that will render the model into legible data for a 3D printer. The design must therefore be exported from Revit into Autodesk’s Inventor or Fusion 360, where the model can be retabulated into a mesh file type (such as STL) and then sliced into a set of instructions that a printer can understand (a G-Code).
Beyond the processing of design data, the designer must also consider spatial constraints of the printing apparatus, the sequence of construction, as well as the material composition of the filament and its resulting structural considerations. WASP, an Italian 3D printing and construction company, has piloted a “Crane” printer with a printable radius of 4 meters and a maximum height of 3 meters that can be deployed on the construction site and print forms in place. The predefined printing area however, means that the designer must consider the segmentation of a total composition, and incorporate the inevitable disassembly and reassembly of the apparatus across the building site. The Dutch architects Houben & Van Mierlo, designers of the first 3D-printed home in Europe, employed a different strategy: printing components in a controlled environment, then transporting them to the site for assembly. Still, the limitations of the printing areas can be seen through the design, with individual walls and roof segments sized within the printable volume of the system, and joined with full height apertures and joints.
Questions surrounding the scalability of 3D printing must also extend to the material employed through the printing system. A cement/aggregate mixture is commonly used with a lesser water ratio. The minimal use of water is essential towards accommodating the additive printing sequence. With each pass of the extruder, the free-standing structure is more dependent upon the rapid curing of the layers below. Shorting the water content of the concrete hastens this curing process; though can result in a weaker mixture and final product. An additional complication of the printing process is that there is presently no way to incorporate additional steel or other structural reinforcements into building elements. While the materials employed through 3D printing technology are beginning to incorporate other materials such as clay, ceramic, and even plant-based fibers, most of these materials are still in early research and development stages and have yet to be thoroughly vetted for structural integrity.
3D printing technology is being described to the construction industry as a means to to save time, money, and as a system with the precision to reduce human error. This may be the case, but only under the right parameters. While 3D printing a structure on site may reduce overall labor costs, the process will call for specialized human resources to serve as robotic technicians and process control engineers; positions that will require intimate knowledge of both the construction and software. Considering this major transformation required for the construction workforce, as well as the design constraints presented by the printing process, 3D printing at this scale still has some research, development, and maturation to achieve.
About the Authors
Emily K. Schwartz is pursuing a masters in Architectural Engineering at the University of Colorado Boulder, and she has earned a bachelors in physics from Carleton College. Ms. Schwartz works as a project manager and is interested in a career in sustainable architectural engineering after graduation.
Charles Newman is an international development professional with more than 10 years of experience working in architectural design, development, and construction management. Mr. Newman founded Unfrastructure Design, LLC, providing consultancy services to non-profits and communities in need.