We’ve all seen and felt the slum conditions in which too many must live and form livelihoods. When the social sector advances to upgrade shacks assembled from scraps or contain ditches of wastewater, could dependency on one single building material also come with strings attached?
From the scattered single-room homes waiting to be absorbed by La Paz’s encroaching El Alto, to a vast landscape of walled compounds packed with yurts ringing Ulaanbaatar’s core, our world’s second-most consumed substance, cement, has become ubiquitous in the built environment.
In the age of climate change and rapid urbanization, reliance on one building material may generate more harm than value. What might social-sector design professionals do to reduce the negative effects of cement?
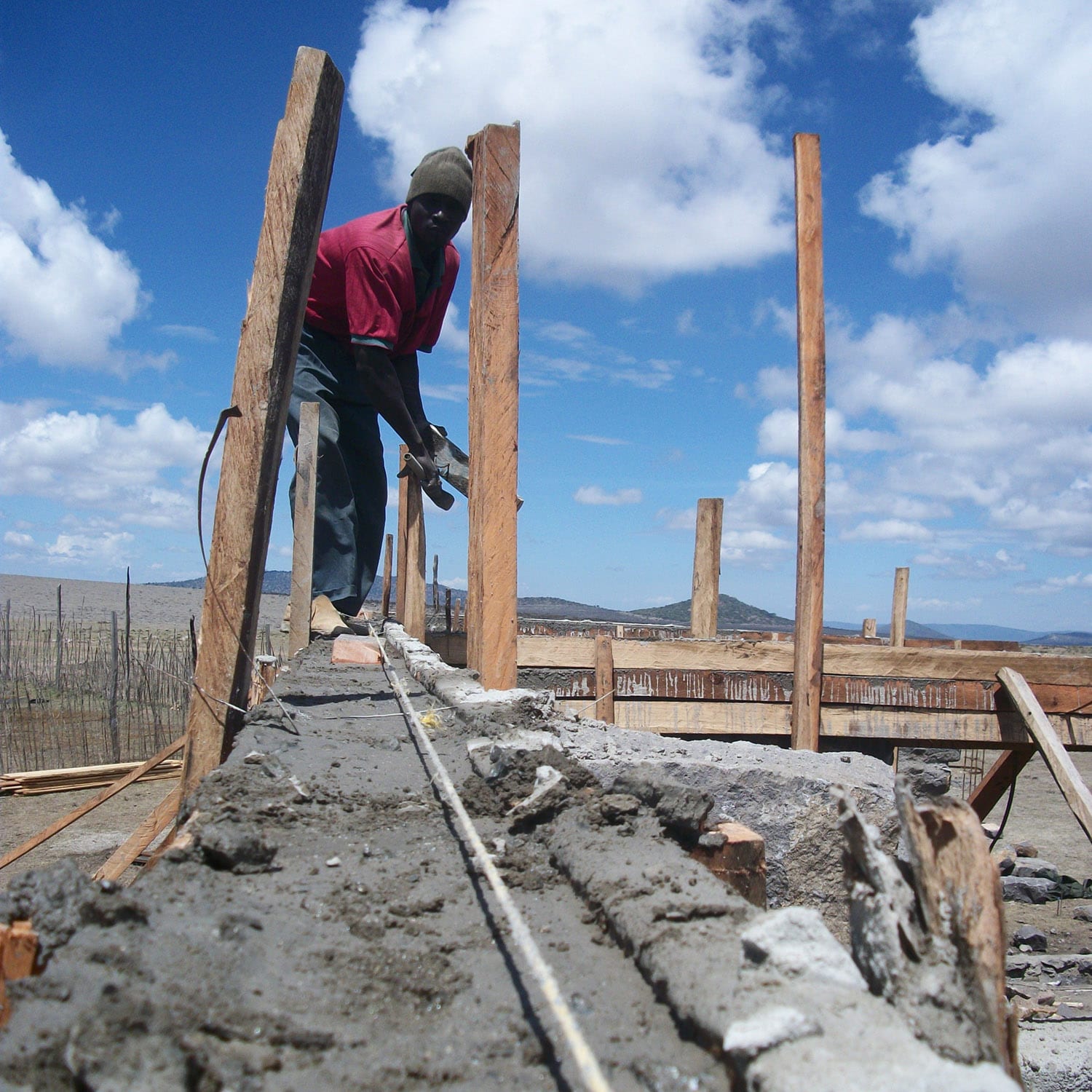
A man works on a site in Sub-Saharan Africa, a photo from a series shot in Kenya and Congo by Charles Newman. See the album on Engineering for Change’s Flickr pages.
But first, what exactly is cement?
While the terms concrete and cement are often used interchangeably, technically, they are not the same. Cement is essentially crushed limestone that has undergone a structural transformation due to superheating. When sand, gravel, and most importantly, water, are added in the right proportions, the mixture (concrete) cures into a single, structural mass. Simply put, cement is the binder in concrete.
Why Cement Is Ubiquitous
In the global North, building projects routinely draw from a diverse array of material choices thanks to a long history of stabilizing macro-level conditions: regulated natural resource management systems, skilled and specialized pools of labor, scalable investment financing, efficient fabrication capacities, reliable energy supplies, expansive distribution systems, and most of all, consumer markets that demand variety and are sizable enough to support new products. In many emerging economies where building material diversity is relatively limited however, cement is among a mere handful of options.
Other reasons concrete is the go-to material for building construction:
- Ease of Handling: Unlike large pieces of steel or glass requiring heavy machinery, a standard 50kg bag of cement can be handled by an individual person as it moves from factory down the chain of vendors to its final work site.
- Versatility: Cement can be mixed into concrete and shaped into nearly every building component imaginable, including foundations, wall blocks, plasters, surface pavers, and roofing tiles. All of which can be mixed and cast on-site, as well as repaired and maintained in place.
- Low Skills and Equipment: Unskilled workers can quickly learn the material’s properties and techniques and use simple hand tools- an advantage in economies where labor costs are low relative to the cost of materials or heavy equipment.
- Fast, Strong and Lasting: Rapid setting times reduce the costs of construction, and few substances rival concrete’s compressive strength. When mixed properly and poured into forms with steel reinforcement, the lifespan of concrete can be limitless.
So what are some of the effects of using cement?
Environmental Effects
Superheating limestone requires constant and intense energy inputs, a power supply most often delivered by carbon dioxide-laden fossil fuels such as coal or diesel.
But it’s not just the energy inputs that cause ecological strain. When limestone is superheated, chemical reactions during its molecular transformation also release carbon dioxide. These two factors explain why the cement industry emits more carbon than the entire aviation industry.
Regulation of the cement industry lags behind most others. In the United States, for example, cement is less regulated than coal. In China, which produces roughly 52 percent of total global supply, cement production is a critical component of an economic and infrastructure development agenda- not just domestically, but regionally as well.
Cement production also uses significant amounts of water to cool heavy machinery, with discharged water impacting local hydrology due to differences in temperature, acidity and various suspended solids. In water-stressed areas, risk of groundwater depletion needs to be constantly monitored, particularly regarding the effects to people, livelihoods, and the ecology of surrounding areas.
In addition to carbon, other heavy metals, such as mercury, also become airborne during cement production, settling onto ocean plankton and concentrating upwards through the food chain.
But cement only makes up a small fraction of concrete. Sand comprises nearly half of the typical concrete recipe, and the global sand mining industry stands accused of wreaking environmental and economic havoc. The “environmental crisis you’ve probably never heard of” is killing wildlife and staunching local trade, The Guardian and The Pulitzer Center on Crisis Reporting write.
In terms of the production of aggregates, the crushing machinery required to produce gravel and sand is also extensive. When capital investments are limited, this lack of capacity puts pressure on natural sources. For example, on Cabo Verde’s Santo Antão island, environmental groups have worked with economically challenged locals against sand extraction in sea turtle breeding areas. Inland, exposed riverbanks are the primary source of sand. Yet, during rainy seasons when rivers are full, sand supply issues become a common, yet unpredictable pinch-point in the timely delivery of building projects.
Economic Effects
While one may assume cement is so ubiquitous because it is cheap, in many low- and middle-income economies, the opposite holds true.
End-user costs: Cement is frequently cost prohibitive for the overwhelming majority of people in countries of the global South. Furthermore, it is often building materials (as opposed to labor or land) that comprises the largest share of housing construction costs. When concrete is the de facto building method, ensuring people’s right to decent, affordable housing becomes highly affected by fluctuating cement prices.
For example, the average price of a bag of cement in the Democratic Republic of the Congo is $30.30 USD- the highest on the African continent. Considering the cheapest private-developer house in the DRC averages $25,000, only 0.3 percent of DRC’s 70 million people can afford such a price.
Large-Scale Production and Political Power
Due to the high energy inputs and equipment costs, setting-up and operating a cement facility involves extreme levels of capital investment and expertise. This is why artisanal or micro-scale cement plants simply don’t exist- the process doesn’t warrant small-scale production.
Furthermore, the immense amount of electricity used for cement production could instead be diverted to households and small businesses who routinely experience scheduled power outages- sometimes daily. These disruptions also disrupt earning and learning opportunities, driving a necessity for back-up generators and diesel fuel to be constantly on hand.
For these reasons, the few who control the means of cement production can amass considerable influence over commodity prices—not to mention political leverage. Cement cartels and kingpins often strong-arm or pay-off politicians when seeking land deals and setting air pollution policies, or negotiating electricity tariff reductions from state-owned utilities. Cement producers seize market share by using political alliances to keep foreign entrants and competitors out.
A GDP’s Achille’s Heel
Yet, when a country is dependent on a single material source for the vast majority of its construction, a debilitating chain reaction can escalate quickly and uncontrollably when supply is suddenly restricted.
In 2012, when a lightning strike incapacitated the Diamond Cement Aflao plant in Ghana, it was one of just two cement plants serving a country of 25 million. After the third week of halted production, the price of a bag of cement in Ghana skyrocketed 60 percent, furloughing both projects and jobs, and forcing cement to be imported from Senegal.
In total this single event registered as a blip in the country’s GDP for the year, and the
World Bank subsequently pressured the Ghanaian government to diversify its cement industry, opening up a long legal battle with industry dominants. Therefore, the very nature of cement production creates highly vulnerable situations for emerging economies.
In terms of long-term financial planning and forecasting, not only are crude oil and energy price fluctuations key factors, but cement also poses an additional moving part for both governments and the private sector. For supply-side housing developers dependent on long-term financing, they are highly averse to committing to high interest loan rates in economic climates where cement price fluctuations could spike. Ultimately, these risks just raise housing prices and limit housing supply- all despite very large demand. Therefore, the idealistic self-balancing laws of supply and demand are especially hindered in the crunchy practical realities of emerging economies.
Material Performance
When examining the performance of cement compared to other materials, one study in Del Rio, Texas, showed that concrete block enclosures actually increase the interior ‘latent’ heat compared to those made with earthen materials, such as adobe.
Cement based homes simply are hotter and colder. Because the material acts as a conduit of heat through the wall, any temperature differences between interior and exterior have a medium in which to pass. In contrast, soil undergoes a very slight, nuanced phase change when placed between two temperature zones, due to vaporization of moisture previously absorbed within the wall. This slows heat transfer, making earthen homes warmer in cold months and cooler in hot months.
As a result, those living in concrete block homes use more air conditioning and energy to maintain thermal comfort. Multiplied millions of times across a city, these choices compound to needlessly increase energy consumption and add to the urban heat island effect.
Durability
Because concrete never decomposes, its durability is often argued by the cement industry as a net environmental benefit. While this may result in longer lasting buildings, in instances when concrete fails or is demolished, it is difficult to recycle the waste to make new concrete. If not used for rubble fill, discarded concrete chunks are simply dumped or buried- in which case those same ‘never-decomposing’ properties create long-term, negative value. While concrete repurposing does exist, few companies have been able to make the process commercially viable. And so, roadside dumpsites persist and rubble graveyards grow through the decades.
So what is being done about cement dependency?
Increasing Production Output
The World Bank has primarily sought to increase domestic production, bringing more cement to global markets in order to bring down pricing through competition and market diversity. State governments have also clamored for increased capacity, seeking their own domestic supply rather than resorting to imports and leveraging any of their own exports.
Increasing Efficiencies
While little has changed in how cement is produced in the last several decades, manufacturers clearly understand that more sustainable approaches will improve their long-term bottom line. The Cement Sustainability Initiative is a collective of cement companies representing 30 percent of global production, and claims to be introducing better practices throughout the entire product life cycle.
Diversifying the Construction Materials Industry
Researchers have long pursued alternative cement products, yet few emerging companies offer viable substitutes or reduced-cement blends that are price competitive and high performance. Regardless, the know-how developed through each of these companies offers incremental potential for gains in sustainability. Yet, the rate of adoption is highly dependent on the degree of climate regulation- as most cement companies won’t invest in new business models unless they absolutely need to, or if the right incentives exist.
Soil-based blocks (stabilized from eroding in the rain due to a small amount of cement) are also gaining traction in many areas of the global South. Once local soil is formed into interlocking shaped blocks via a manual or hydraulic machine, these compressed earth blocks, or CEBs, require no mortar in between courses, allowing them to dry stack, speeding the rate of wall assembly as well as adding a degree of seismic resistance.
Both machine types are portable, so construction costs can be reduced through the use of localized, less-specialized workers. The bulk of building materials can be extracted directly from the site / immediate area, rather than importing and transporting materials from far flung places.
Overcoming Cultural Barriers and Social Stigmas
One frequent impediment in the adoption of alternative building materials is local social stigma towards traditional and earthen materials. In many developing countries, where up to 90 percent of homes are self-built, industrial materials are perceived by the vast majority as ‘more durable’ or ‘advanced.’ Conversely, traditional materials are often considered ‘inferior’ or ‘for the poor,’ even in cases in which the industrial materials are of poor quality, or poorly constructed.
When architects are able to work in partnership with underserved communities, the combination of roles and sense of co-ownership can be highly influential in altering these types of social perceptions. By actively listening to community members and understanding cultures and lifestyles, architects can serve as cultural interpreters, blending technical and social cues into re-imagined and re-composed solutions that both satisfy practical needs and are spiritually harmonious.
Public buildings, schools, play areas, and community centers that are highly visible or placed in prominent locations in a community, can provide tremendous inflection opportunities to alter mindsets, build local capacity in alternative building techniques, and most of all, instill a lasting common identity and sense of dignity and pride.
This local ripple-effect, explained by architect Anna Heringer here as a ‘Catalyst for Development’, is being adopted by a growing body of practitioners from multiple sectors. These values go well beyond the functional and practical needs of a community, far beyond a fulfillment quotas of housing units. This approach to development is also not based on introducing new products or magic gizmos per se, but rooted in a human-centered mindset and approach.
Therefore, we can identify the barriers and harm that dependency on a single, ubiquitous building material can make on our built environment, our air, our economies, our politics and our social order. Eliminating cement usage entirely is, of course, impractical. Our challenge instead is to reduce its use and favor locally sourced and traditional materials whenever possible. We will need to change our perception toward the built environment and toward each other: how we create, how we build, and how we collaborate in more sensible and sensitive ways. This approach is what we need to disseminate, this is what our supply chains should support, and how our markets should operate.
The approach needs to become ubiquitous. As much so as cement is today. If we can take this focus, no single building material can ever have an outsized effect on our collective wellbeing.
About the Author
Jason Moses is a Contributing Editor at Engineering for Change, a social architect, construction project manager and founder of CommonThread.com. CommonThread is a social enterprise that makes community-driven approaches the primary means for upgrading slum conditions and informal settlements.