Communities in emerging economies can convert their waste plastic into a fuel oil that can be used as a drop-in substitute for diesel or kerosene. The University of Kentucky Appropriate Technology and Sustainability (UKATS) Research Group implemented a pilot test of the process in Kampala, Uganda, in collaboration with Makerere University and Institutional Energy Solutions.
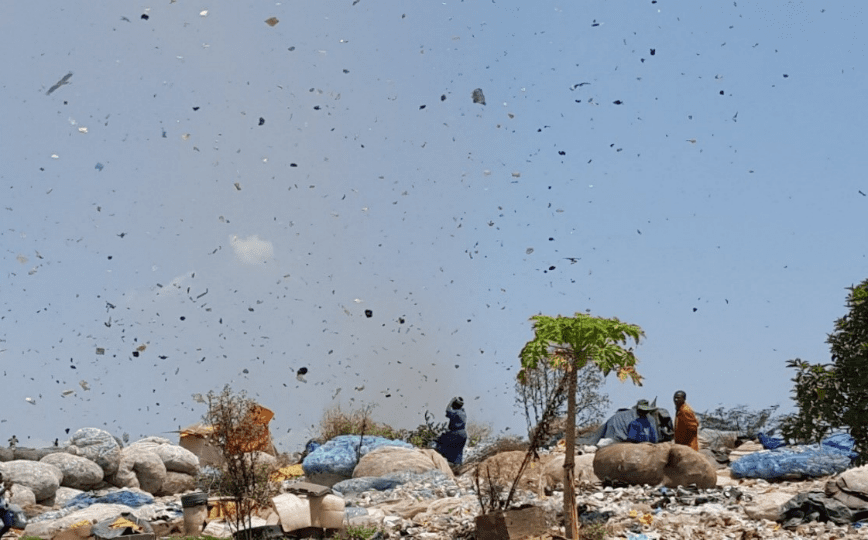
Trash blows among the waste pickers at the Kiteezi Landfill in Kampala, Uganda.
Lighter, stronger and cheaper than other materials, plastics really are a miracle of modern chemistry. Despite their benefits, however, there is an ever-increasing mass of mismanaged plastic waste damaging the global ecosystem.
Only a tiny fraction of plastic waste is actually recycled. In industrial economies with well-developed infrastructure, most plastic ends up in a landfill. In developing countries and places without easy disposal options, plastic waste often ends up on the ground and in waterways.
Once waste plastic enters the ecosystem it persists for decades or even centuries. Much of this plastic waste ends up in the ocean. According to the Ellen MacArthur Foundation, by 2050 the mass of waste plastic in the ocean will exceed the mass of fish.
Reframing the problem
To combat the rising issue of waste plastic, a new approach is needed. The traditional manufacturing paradigm is based on a “Produce Distribute Consume Discard” model. As an increasingly popular alternative, the Circular Economy addresses the design phase to ensure that products retain value after they are used or even broken. The concept encourages designers and producers to consider end-of-life issues when developing new products and processes.
Through that lens, we could say that plastic is discarded because it does not have value.
This way of thinking could transform the problem of plastic waste. Through that lens, we could say that plastic is discarded because it does not have value.
A decentralized circular economy
Plastic must be given a value so that it isn’t discarded. And in developing or resource-limited regions, that value must be recognized locally, because supply-chain constraints favor localized solutions. That means decentralized collection and decentralized use of plastic waste.
We propose the Locally Managed Decentralized Circular Economy for Waste Plastic. Imported manufactured goods enter the cycle as the initial feed source. The plastic is used locally, collected post-use, then used as raw material locally to produce goods that can then be sold back to the community. The only output from the perspective of municipal solid waste is any material that gets discarded because it is either not collected, or can’t be used.
The key here is that everything is local. Collection, production and use are all managed in the local community. Of course this limits the scope of manufacturing, but has a higher likelihood of success when implemented. The real benefit is that this approach does not require sophisticated infrastructure and provides a local incentive for waste collection.
How plastic to fuel works
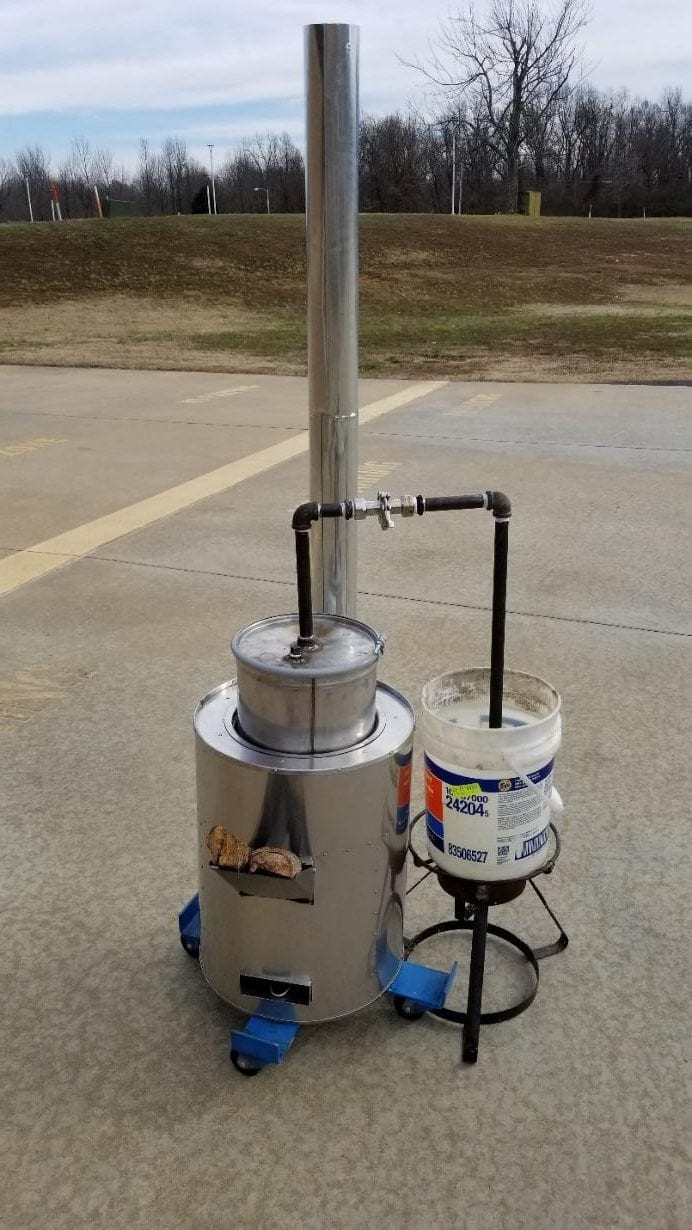
The UKATS Group developed this device to slowly pyrolize waste plastic using the heat of burning wood.
A technology that can be deployed as part of a locally managed decentralized circular economy is the conversion of waste plastic in a fuel oil, suitable for use in a diesel engine or a kerosene cook stove. Plastic polymers like High and Low Density Polyethylene, Polypropylene and Polystyrene and be converted into a liquid fuel by a process called thermal decomposition, or a slow pyrolysis. During the process, the long chain polymers that make up the plastic break down into smaller and smaller molecules, eventually reaching a molecular weight and heating value similar to that of diesel fuel or kerosene.
One kilogram of plastic can be converted to one liter of fuel oil. The process is simple and can be designed to perform in a resource-constrained region.
This fuel can be directly used in an unmodified diesel engine. Using this process, 1 kilogram of plastic can be converted to 1 liter of fuel oil. The chemistry is simple and a process can be designed to perform in a resource-constrained region. The UKATS research lab developed a device constructed from materials that are widely available in developing countries. Our device slowly pyrolizes plastic waste using heat produced by burning wood or other biomass.
The plastic-to-fuel process is particularly suited to an appropriate technology solution. The chemistry is simple and the operation can be carried out on a small scale with limited technical expertise. Developing countries may even have an advantage over the developed global West. In a developed economy, most waste is unsorted, which makes the process more challenging. In emerging economies, people are able to sort waste and retrieve the appropriate plastic easily.
We have referred to the process of converting waste plastic into fuel oil as Trash to Tank, or 3T.
Trash to Tank (3T) vs. recycling
The 3T process differs from other recycling efforts in that the plastic is completely consumed. Although we don’t mean to suggest that recycling efforts are in anyway negative, they don’t remove the plastic from supply chain. Eventually, recycled plastic will reach the ecosystem. Other efforts like remanufacturing the plastic as a building material or aggregate for roads are also positive, but only serve to delay the eventually migration of plastic to the ecosystem. Of course, using the plastic as a motor fuel does release CO2 into the atmosphere, but as our previously published research shows, it is less than what would be released from fossil-based diesel fuel and contains no sulfur emissions.
3T provides an economic incentive for underserved communities to address their waste plastic problem themselves.
The 3T process benefits people by contributing to clean communities, prosperity by providing business opportunities for local entrepreneurs, and the planet by diverting plastic from entering the ecosystem and producing a cleaner burning fuel than fossil derived options. In short, 3T provides an economic incentive for underserved communities to address their waste plastic problem themselves.
Implementation of Trash to Tank in Uganda
The UKATS group, the Department of Agricultural and Biosystems Engineering at Makerere University, Institutional Energy Solutions in Cottage Grove, Oregon and the Rotary clubs of Paducah, Kentucky and Kampala North have worked together to implement a pilot test of the 3T concept in Uganda. The team selected and trained a recipient of the processor, who then began producing fuel from locally gathered waste plastic and selling it as a side business.
Since July 2018, the recipient has been processing waste plastic four to five times per week, producing 20–25 liters of fuel weekly. Due to the success of the pilot test, the project will be expanded in 2019.
Path forward
The team plans to expand the project in Uganda during the summer of 2019. Six processors will be distributed around Kampala. Additionally, the team is working with the Uganda Bureau of Standards to have the fuel certified as an over-the-road fuel. This will help with the broad implementation of the project.
About the Authors
Jeff Seay is Professor of Chemical Engineering at the University of Kentucky and PI of the UK Appropriate Technology and Sustainability research lab.
Chandni Joshi and Ronald Kizza contributed.
I’m curious about the emissions from the process – that’s a large smokestack, do you have any scrubbers in there?
Hi Anna, Thanks for your question. The energy to run the process comes via a rocket stove manufactured by InStove (www.instove.org) in Cottage Grove, Oregon. This wood fired stove is incredibly efficient. The stack gas produced doesn’t actually need any scrubbing. The InStove rocket stove reduces particulate by 90% versus an open fire and produces no visible smoke.
There have been many plastic->oil “solutions” before, but each of them has had at least one major problem slowing adoption – as I understand it, and applied to what I read above for your system, the typical issues are:
a) a lot of energy required to run the process – for example the system from blest.co.jp used more electricity to run than the diesel produced could have generated (in locations where most electricity came from diesel). Yours is in a wood stove, but the energy balance isn’t mentioned, how much wood does it take to make a liter of diesel-substitute?
b) good separation required e.g. working on only one kind of plastic. This can add significant cost, especially for soft plastics which are rarely marked. You don’t mention how pure the input stream has to be?
c) seriously toxic waste resulting from the unconverted plastic, all the halogens in the plastic end up in the waste – unless the separation mentioned above is done. Is there a waste issue in your process ?
d) further refining steps – some of the processes produce the equivalent of crude that has to then go in a “normal” refiner, making them only suitable for large scale use – sounds like this isn’t an issue for you. .
I’d be interested in how your solution stacks up against each of these.
What are the time and temperature involved? Is there any chance that a solar concentrator stove could be used instead of a wood burning stove?
Hi Mitra, Great questions! Several of them are addressed in a paper we recently published in the Journal of Environmental Progress and Sustainable Energy (DOI:10.1002/ep.13086). As our published work demonstrates, the energy balance is positive, even for wood fuel, and the total CO2 emissions are lower than petroleum derived fuels on a total life cycle basis. As for the feed stream, our process only uses HDPE, LDPE and Poly Propylene as inputs. Other plastics, as you correctly point out have potentially toxic emissions. The good news is that these plastic are easy to identify. Suitable plastics float in water, where as unsuitable plastics sink. That’s how we train users to tell the difference. Since we only use select plastics, no further refining is necessary. Our process isn’t a magic bullet, of course, but we believe that is a sustainable solution for developing regions. Thanks for your interest!
Hi Newt, the temperature required is about 450C. The time of course depends on the heating time and batch size, but for our process the process runs for about 3 hours and begins producing within about 20 minutes. As for solar concentration, I don’t know of a small scale unit that gets up to 450C, but if there is one it could certainly be used! Thanks for your questions!
Interesting did you see anyone do this plastic separation in your field tests ? From the one project I saw in southern India plastic separation was expensive and significantly added to the cost. For the flotation method it sounds like they need a shredder which adds the questions of can you shred plastic bags, and is the energy cost of the shredding included, and you list LDPE, HDPE and Poly Propylene but I thought styrofoam (not listed) also floats ?
Notably missing from the paper is any kind of costing, at a reasonable estimate of production cost of the stove, and the shredder, and the cost of labor for separation & production what kind of cost do you think is achievable per liter of fuel ?
Thanks for making the paper open-access, closed access papers being largely irrelevant to the field of international development ! For those who don’t speak DOI, the paper is at https://onlinelibrary.wiley.com/doi/full/10.1002/ep.13086
Hi Mitra, For our field trials, the users were trained to separate the plastic. In Uganda, there is a thriving economy for people working in the trash dumps picking and separating trash of all types. So far, the issue of separation hasn’t caused us a problem, but we are working with NGOs to select those who are using the process, so we are able to do the training up front. Styrofoam, as you mention is a bit of a bugger. Polystyrene does not float but styrofoam does. Although it certainly makes acceptable fuel, the concern is cyclic aromatics in the product, which are of course often toxic. We advise operators not to use it, but it is a source of risk. We haven’t published the economics in full because we are still evaluating, but a preliminary case study can be found here (DOI:10.1002/ep.13086). I can share with you that the pilot studies are looking positive from the economic standpoint, but are some regulatory hurdles still to cross before this can be fully commercialized. So far our work is classified as research but broad scale implementation requires regulatory approval. We hope to be publishing a full economic assessment after our planned expanded field trials this summer. Thank you again for your questions and interest in this work.
Hi Jeff, This is amazing. Is there a way we in India can get access to this pilot program and move it real Plastic Fuel pumps for villages.. I would be very keen to get it launched.Secondly is the a way to use Solar heat for ‘slowly pyrolizes plastic waste using heat instead of heat produced by burning wood or other biomass’. While collecting plastics 1 Kg ( is there specific type of plastic ) is there any restrictions. What is the possibility to make it on a larger size than the size of equipment shown.
Hi rajanbh24tech, Absolutely! In fact we pilot tested this process in Tamil Nadu a few years ago. We used the fuel for irrigation pumps. The plastics that we use are polyethylene (HDPE and LDPE) and polypropylene. Although polystyrene makes good fuel, there are some potential toxicity concerns with the off gas. For that reason, we stay away from it. Concentrated solar might work, if you can achieve the proper temperature. I’m not familiar with a solar stove that can get hot enough, but in principle it could work. Scale up is also possible, but I haven’t run the economics calculations, so I can’t yet say if it would be profitable. I would be happy to provide more information to you.
I am very interested to try this processor in my country as we also have a huge plastic waste problem. Please advise and help me on how to obtain this processor and receive training on how to operate and maintain this processor unit.
Thank you.
Mr. Oveai Morea