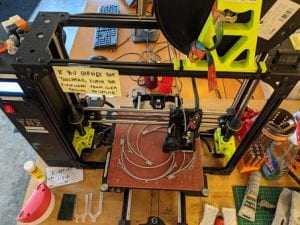
Photo: Timothy Prestero / Design that Matters
Manufacturers and hobbyists have turned their 3D printers to the challenge of restocking the depleted global supplies of medical and personal protective equipment. Around the world in the hotspots where hospitals are overburdened with patients who have coronavirus, 3D printers are supplying parts and PPE, as protective equipment is often called. It’s the kind of work that saves lives. But the grassroots nature of this manufacturing movement makes standards enforcement difficult.
Many organizations involved in printing parts and PPE offer the disclaimer that their designs should serve only in emergencies. There may be a way to design and manufacture these kinds of products within vetted safety and performance standards, however.
“Manufacturers are eager to provide PPE and other devices and equipment that are in short supply. Many unvalidated designs already exist in numerous online repositories, but manufacturers – especially those who traditionally do not produce medical products – are looking for guidance on standard, validated designs and materials to use,” Christine Reilley, Senior Director of Strategy and Innovation at the American Society of Mechanical Engineers, told Engineering for Change. (Disclosure: ASME is the parent organization of E4C.)
For direction, manufacturers in the United States can turn to America Makes, the US National Additive Manufacturing Innovation Institute. This public-private partnership has launched a COVID-19 response platform. Working with the US regulatory body the Food and Drug Administration and other entities, America Makes is building a repository of requests from healthcare providers and medical device designs from additive manufacturers (3D printers).
“This is a movement underway to provide manufacturers with the standard designs they may need to produce medical devices and equipment,” Ms. Reilley says.
See COVID-19: Health Care Needs and AM Capabilities Repository
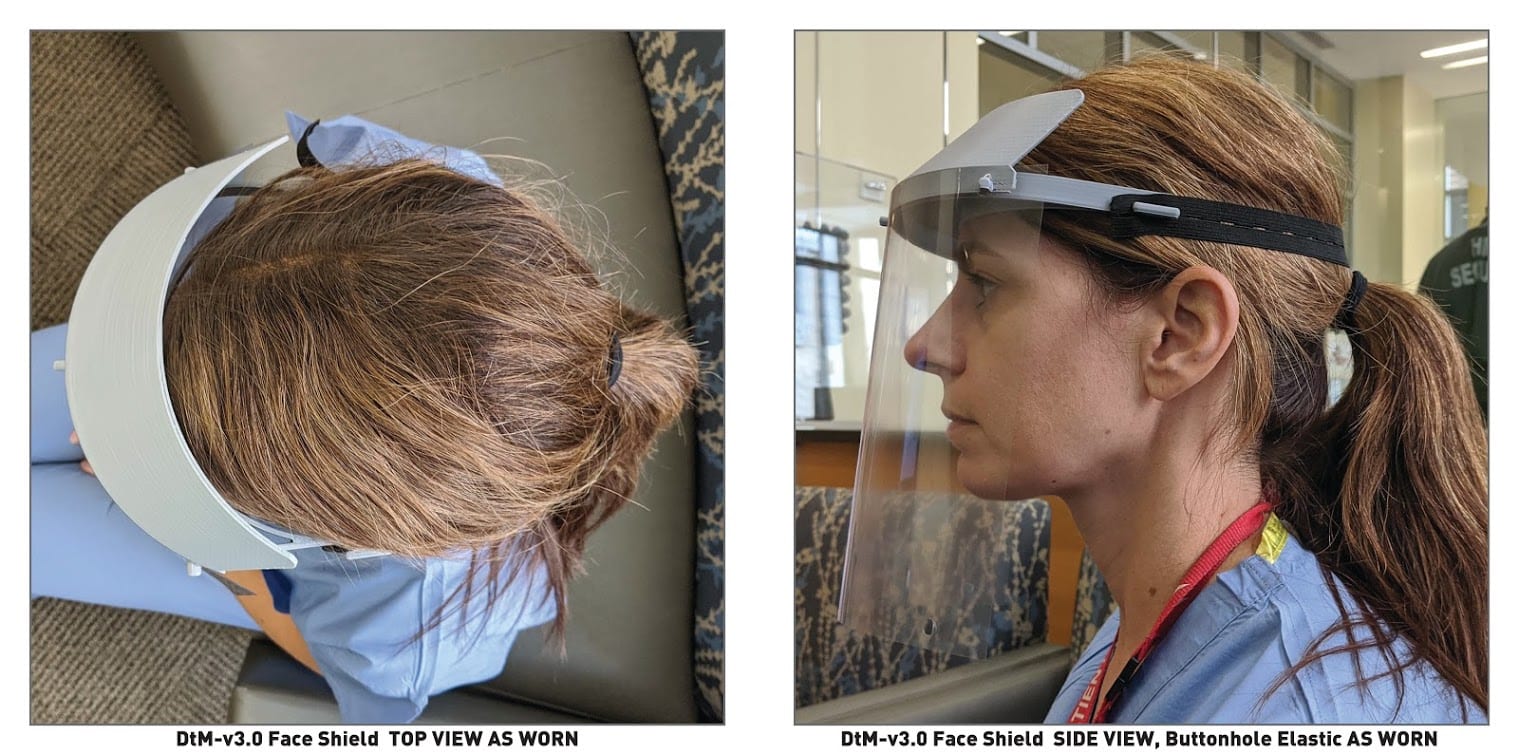
Photos: Timothy Prestero / Design that Matters
The non-profit Design that Matters has mounted a separate effort to improve the quality of 3D-printed PPE. DtM’s global health medical device designers released schematics for a clinically tested 3D-printable faceshield under a Creative Commons license. Products for hospitals in developed countries are outside of the organization’s purview, as DtM’s designers ordinarily build devices for low-resource settings. But circumstances have changed.
“The speed of the coronavirus pandemic is turning all clinical settings into low-resource settings,” the organization wrote in a statement.
In the last week, we have assembled a team of over forty experts in design, engineering and medicine with volunteers from Spark Health Design, Microsoft, and Boeing, and clinical experts from Mass General Brigham, the University of Washington Harborview Medical Center and the UW Medical Center at University campus. Working nonstop in groups spread across the country, we have blasted through three very fast cycles of prototyping and clinical testing. The final design, DtM-v3.0, along with instructions for fabrication and assembly, have been officially released on the NIH website.
See DtM’s faceshield design, including CAD and STL fiels, on the US National Institutes of Health website.
Call to Action
DtM issued a call to action with points that E4C would like to amplify.
- To those who are making face shields, consider using this design in whole or in part.
- To those who know healthcare workers, please tell them about this design and encourage them to contact DtM for access.
- If you have access to a 3D-print farm or higher-volume manufacturing processes like injection molding, please contact DtM.
- If you have a 3D printer, print these shields and please post a picture!
As always, please stay safe. Jeremy Hanson, co-founder of Seattle Makers, demonstrates workshop safety with disinfection methods and tools to reduce the need to touch surfaces and risk exposure to coronavirus. Mr. Hanson’s maker space is also producing 5000 face shields of a simple design built from mylar, EVA foam, tape, staples and elastic. Here’s a how-to video. And please see the workshop disinfection demo below.