The United States has more total wealth than any other nation and even here we have a shortage of personal protective equipment. On the bright side, the incredible global maker community has created an explosion of face shield PPE designs for COVID-19. Design that Matters and Spark Health Design have built on lessons from our experience designing medical devices for low- and middle-income countries to design the first face shield recommended by the US National Institutes of Health.
What’s Good and What’s Possible: An Inspired Engineering Response to the Pandemic
COVID-19 is turning the whole world into a low-resource setting. To design PPE for COVID-19 in that context, we can learn from healthcare professionals who work in communities affected by poverty. PPE is often designed to be disposable, and that is how it is used in wealthy countries that are not experiencing a medical crisis. Cleaning PPE that was intended to be disposable is an everyday reality in many places around the world. Even in the midst of the Ebola crisis, healthcare professionals in Liberia had to wash and reuse rubber gloves that ultimately ran short (Hinshaw 2014, Wallstreet Journal). There is enough wealth in the world to ensure there are never gaps in medical supplies anywhere in the world, but health inequity persists.
Now, the United States is experiencing the dire consequences of gaps in medical supplies. Though we wish the country had stockpiled sufficient supplies of disposable PPE, when the PPE supply gap became apparent in China and then Italy, we realized the equipment would be reused during this period of emergency.
Read more about Elizabeth Johansen’s approach to designing medical technology for global health: What to Do When FDA Approval Doesn’t Mean a Medical Device Is Safe
To design a reusable, washable face shield, we started with the Prusa R2 3D-printed design. We maintained many of its excellent features such as universal pegs that accommodate a variety of headband straps, and a dual-ring design that keeps the face shield offset from the face to leave room for face masks and glasses, while still holding securely to the head.
Our next step was to conduct background research to inform the requirements for a reusable face shield. This included a literature review and gathering guidelines from the US Food and Drug Adminstration and the US Centers for Disease Control that explain how healthcare professionals should approach the reuse of PPE that is normally a single-use disposable. From Chan et al 2018, we learned that infectious aerosols and splatter could enter from the top of a face shield.
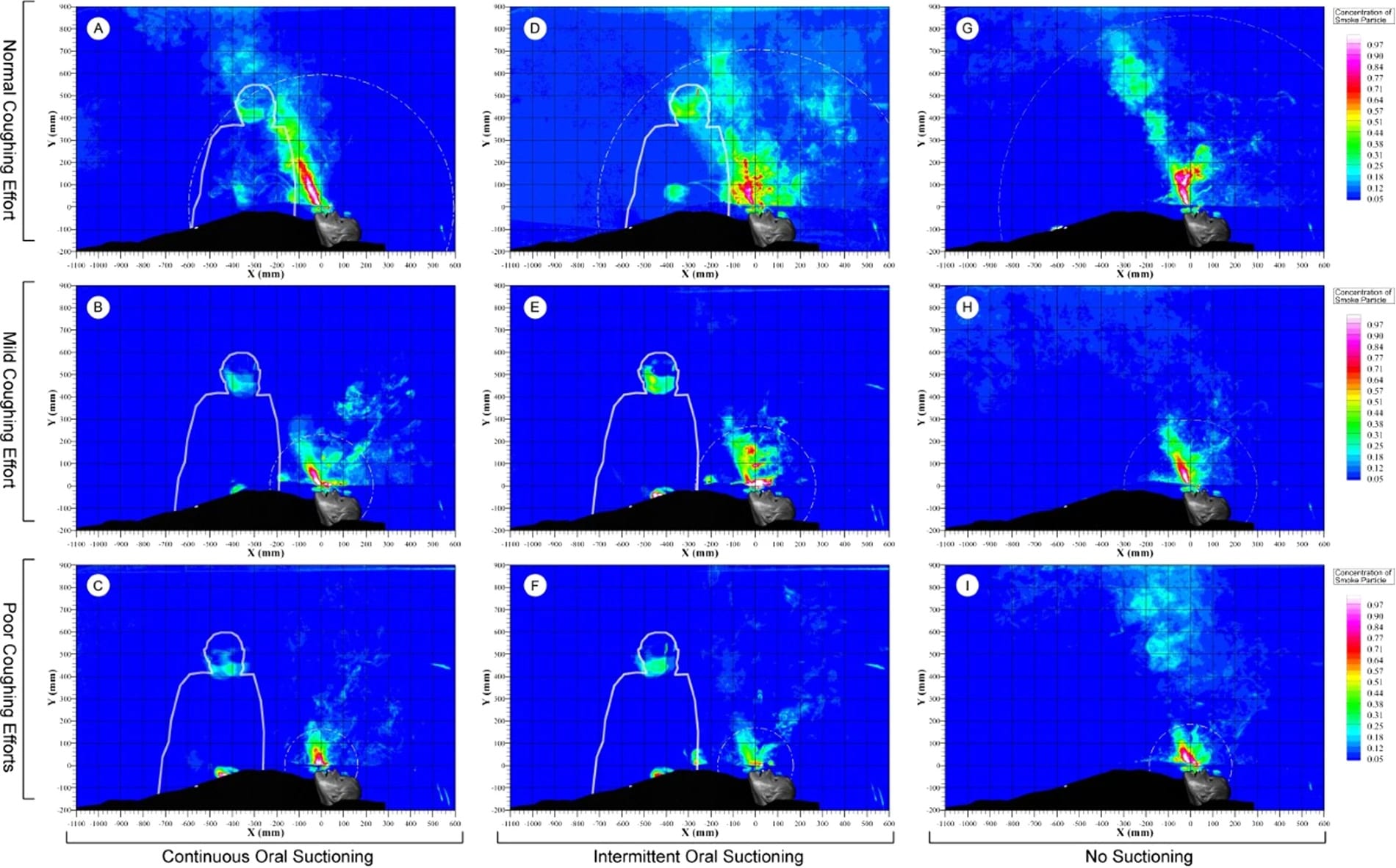
A simulator reveals the dispersion of air after a patient coughs while lying face up. Image: Chan et al, Nature 2018 (open access)
In response, a DtM volunteer from Microsoft suggested adding a backward visor to the top of the Prusa R2 design to limit aerosols and liquids from above while still maintaining top ventilation to reduce fogging and enabling it to conform to the head.
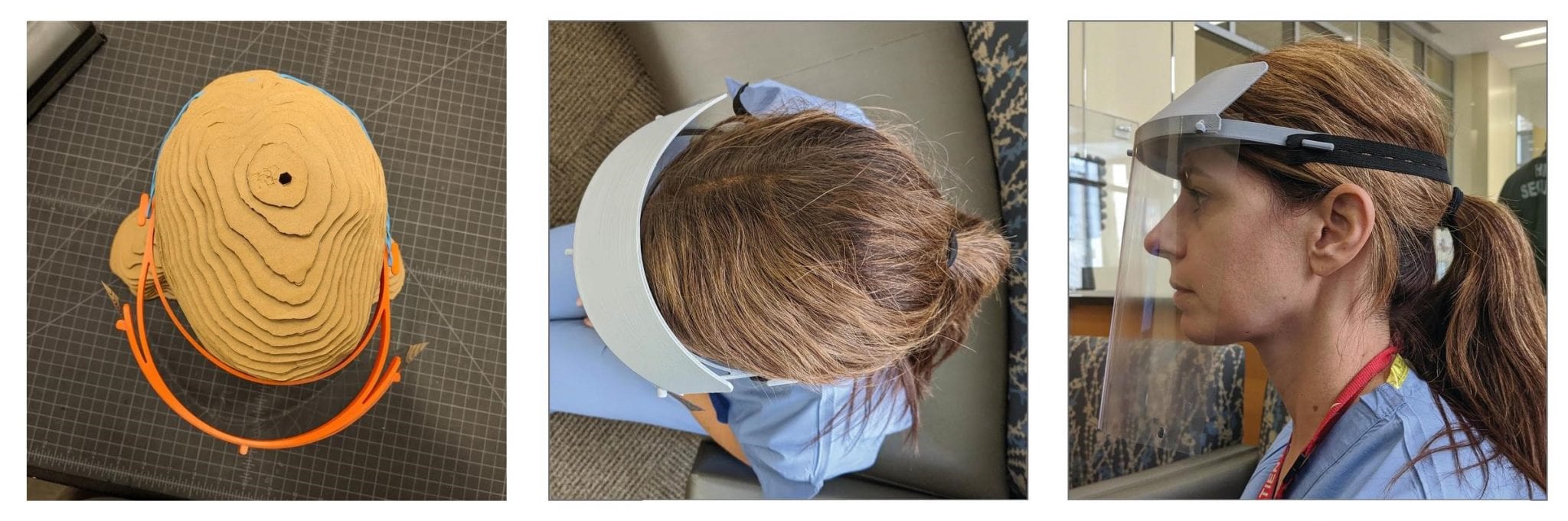
Left to right: Prusa R2 top view, DtM-v3 top and side views as demonstrated by a nurse at Harborview Medical Center. Photos courtesy of Design that Matters
The effort to provide reliable PPE reaches beyond a single face shield design. We made our background research immediately public through dissemination in the Open Source COVID-19 Medical Supplies and MGB Innovations Groups and on the DtM website to guide others in designing their face shields. Access our background research here.
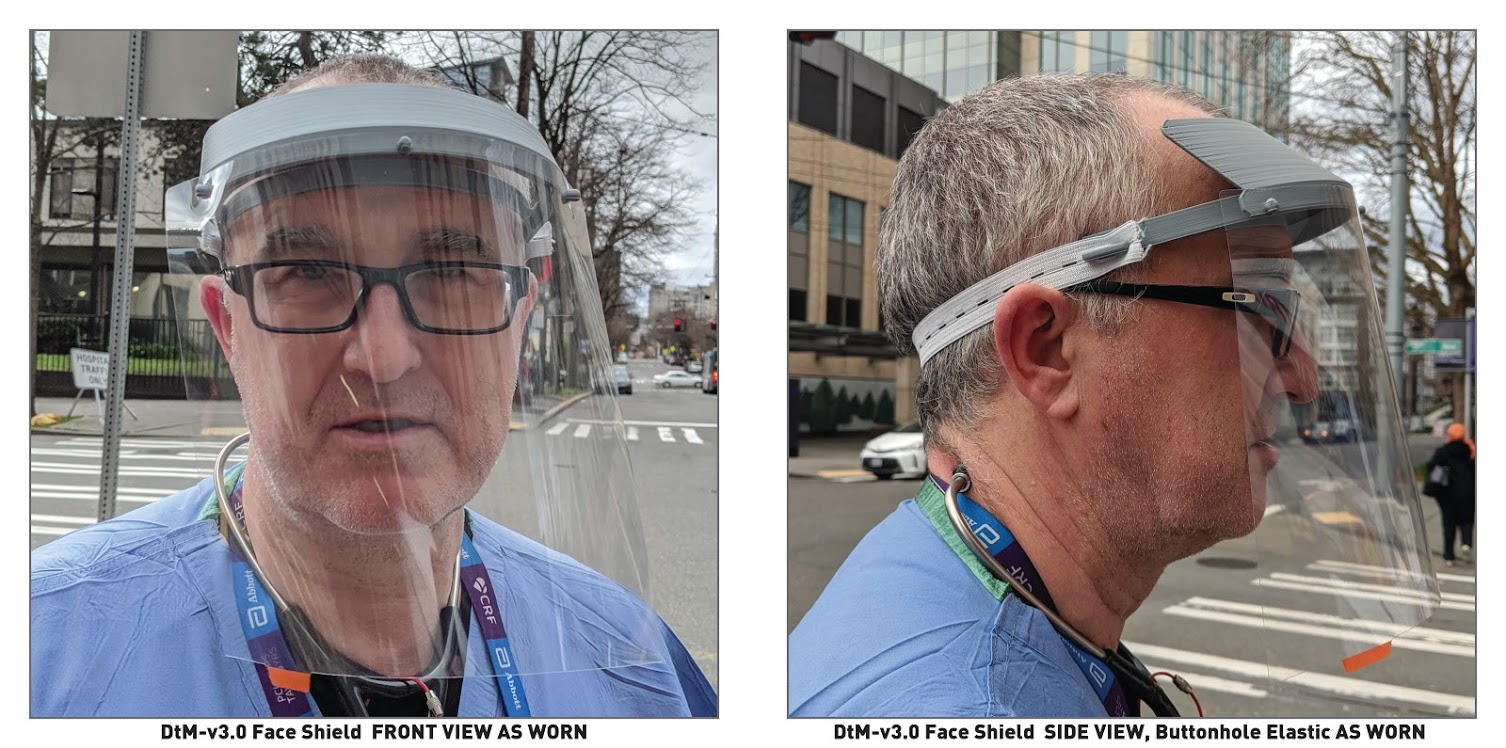
Dr. Graham Nichol demonstrates the face shield’s fit outside of Harborview Medical Center in Seattle, Washington (USA) where he is the Director of Pre-hospital Emergency Care. Photo: Timothy Prestero / Design that Matters
With various iterations of prototypes in hand, we gathered feedback from healthcare professionals in Seattle and Boston. This process of considering the needs of many stakeholders is called human-centered design. Nurses, doctors, and infectious disease experts from University of Washington Harborview Medical Center, the UW Medical Center at University campus, and Mass General Brigham provided feedback and piloted the final versions over multiple shifts.
One insight we discovered from engaging with stakeholders is that those who must take the most risk by working on the frontlines, have the least control over their PPE supply. DtM and Spark Health Design are accustomed to designing global health medtech that considers the limited supply chains of low and middle-income countries. Amidst the global supply chain disruptions of the COVID-19 crisis, the DtM-v3 face shield enables 3D-printers to respond to local needs using a variety of resins and office supplies; no laser cutter required. We changed the peg spacing on the Prusa R2 to empower essential workers to use a three-hole punch and a clear report cover from the office supply store to replace the transparent shield if scratched or dirty, putting the control into the hands of those who need PPE the most.
In designing for low-resource settings, we are often designing for swamped hospitals with low staff-to-patient ratios. Echoes of the same concerns came in a recent U.S. COVID-19 face shield working group where healthcare professionals expressed concerns about foldable face shield designs requiring multiple minutes to assemble. 10% of an HCP shift could be lost to assembly if it takes 2 minutes to disassemble and reassemble a complex face shield to clean after every patient. Based on the Prusa R2 architecture, the DtM-v3 transparent shield rapidly snaps onto the headband frame. It has no moving parts; from designing equipment for rural hospitals, we learned moving parts are the first to break.
To help fabricators comply with the April 9 FDA Emergency Use Authorization for face shields for medical use, DtM and Spark Health Design launched an updated, open source, graphical instructions for use for the DtM-v3 that can also be adapted to other face shield designs. Thanks to DtM graphic design volunteers SchmietaPlus and Natalya Zahn, it can be found here in an online Google presentation.
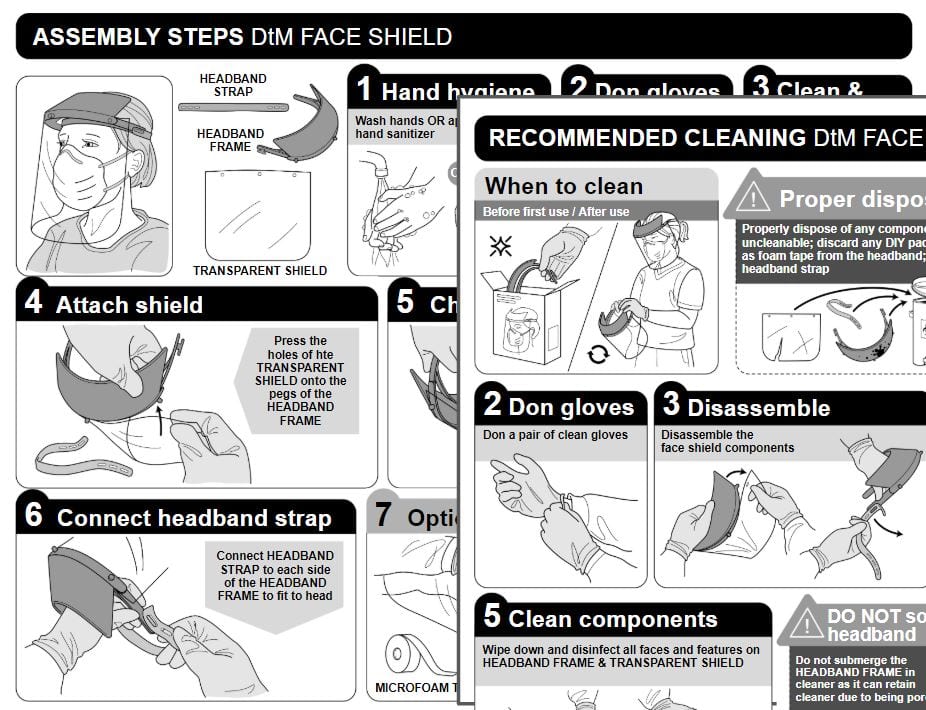
These graphical instructions support fabricators and manufacturers in meeting the requirements of US Food and Drug Adminstration Emergency Use Authorization for Face Shields.
The DtM-v3 was launched in only one week thanks to the efforts of over 80 volunteers. It is currently being fabricated on campuses and in homes around the U.S., and Canada. In addition, Boeing is using their thirteen additive manufacturing sites across the U.S. to fabricate face shields for distribution by FEMA (video, press release). Anyone who wishes to 3D-print the same NIH-recommended DtM-v3 face shield can access the files in NIH’s site.
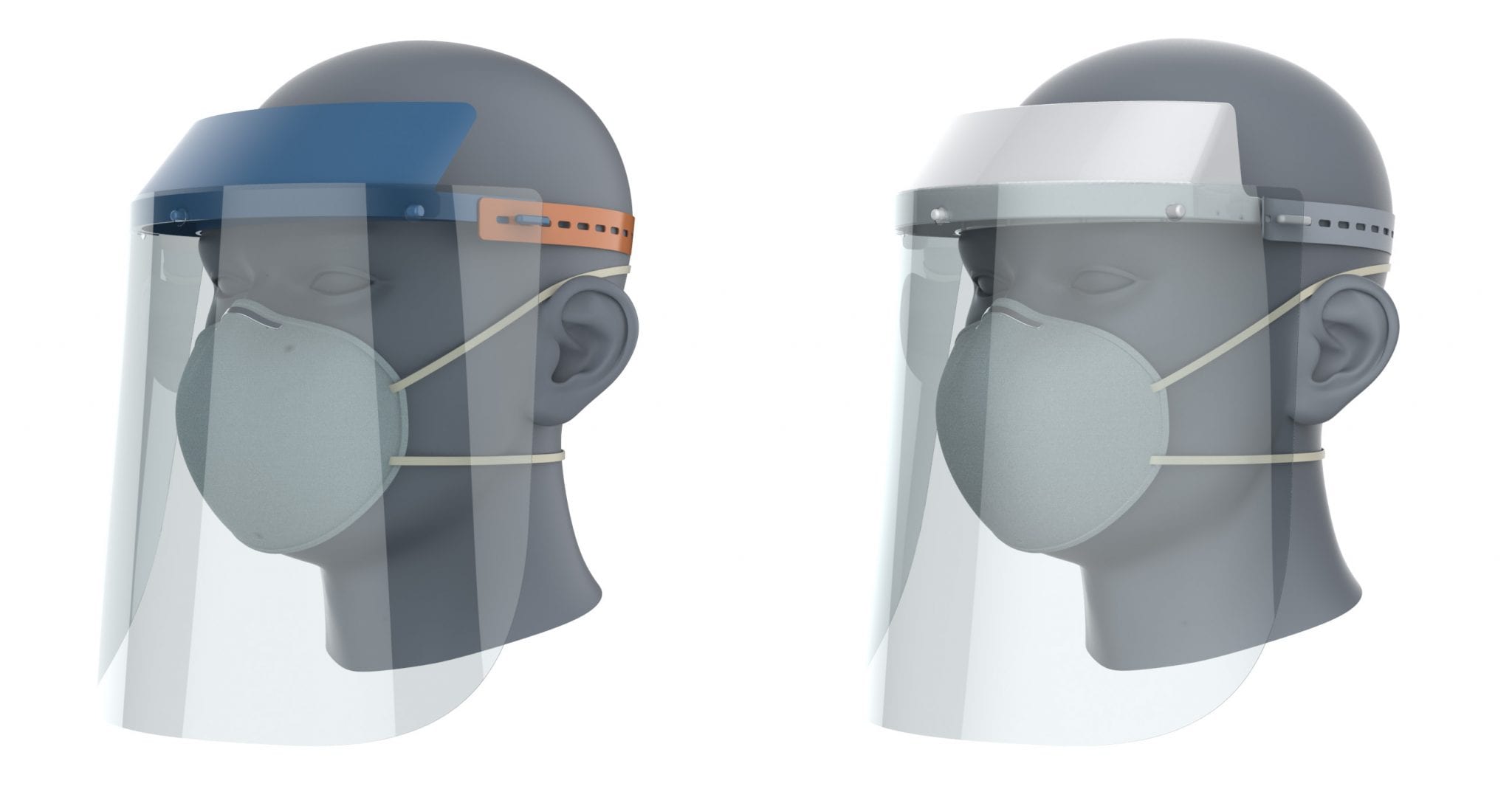
Left to Right: The DtM-v3 for 3D-printing and the DtM-v4 for volume manufacturing. Renderings courtesy of SchmietaPlus
3D-printing can be used to make 1000’s of face shields; volume production can achieve even greater scale. Thanks to a collaboration with Boeing, Downstream Therapeutics, Impact Washington, GlobalTech Plastics, Aero-Plastics, Tool Gauge, Trelleborg Sealing Solutions, and Teknor Apex, the face shield has been adapted to volume production methods of injection molding, casting, die cutting, and extrusion. The new DtM-v4 also adds a protective wall to the top sides of the visor, and eliminates the small corners between the dual rings to make it easier to wipe down. Working together, we are pleased to provide the open source, NIH-recommended DtM-v4 face shield including a free, turnkey package of design files, instructions for use, labeling, packaging, and quality systems advice for use by any volume manufacturer. Manufacturers are currently producing the DtM-v4 in the pacific northwest and we look forward to enabling others to scale this clinician-approved, reusable face shield design that puts the power into the hands of those who need the protection the most during this PPE supply gap. Access the DtM-v4 turnkey package for volume manufacturers here: https://3dprint.nih.gov/discover/3dpx-013830.
Learn more about the Face Shield at Design that Matters’ website: designthatmatters.org/covid-19.
And learn about Spark Health Design’s human-centered approach to the design of medical technology for global health: sparkhealthdesign.com.
About the Author
Elizabeth Johansen is a former Contributing Editor at Engineering for Change, the founder of Spark Health Design and an instructor in the Affordable Design and Entrepreneurship program at Olin College of Engineering in Needham, Massachusetts (USA).
Hi Elizabeth,
I Have a face shied design that only needs a soda bottle!
Whats needed
3″ hole saw, drill, razor knife, a little fun task, and a face to protect.
But I do not know yet how to post ideas on E4C.
I did join the Pact-covid challenge on HeroX
right now, we are the only team in this group.
https://www.herox.com/PactCOVIDResponse
https://www.herox.com/PactCOVIDResponse/team/10696