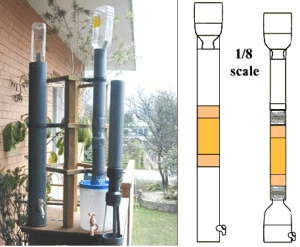
Filters filled with crushed ceramic granules may be easier and cheaper to make than other ceramic water filters, and just as effective. Images courtesy of Reid Harvey / Silver Ceramic Systems
Reid Harvey may have hit on the simplest method yet for manufacturing effective ceramic water filters, the packed particle bed. The key is the particles, which are ground ceramic granules treated with silver nitrate to kill pathogens. Rather than bother with firing whole ceramic pot-type water filters or candle filters, the packed particle bed filter simply packs a container with ground ceramic granules, sieved to size.
For years, Harvey, a ceramic industrial designer, taught ceramic candle filter manufacture in rural villages in Nepal, Nairobi and other countries before he realized how to simplify the process.
The candle filter works. It’s a porous ceramic tube, also treated with silver nitrate. Properly made, it can catch most of the sediment and microbes in contaminated water. Harvey trained potters in Nairobi in candle filter firing, and they have since produced and sold 5000 filters to off-grid residents in their communities. Flower pot filters, like the kind that Potters for Peace promotes, also work, and effective programs worldwide are training people in their manufacture as well.
Harvey’s idea simply strips down the process, while using many of the same materials and construction methods.
“I was working with someone who was producing candle filters and I just thought to myself, why do you need to fire the granules together, why not just put them together in a pot?” Harvey told E4C.
Grog and shale
To make a packed-particle bed (PPB for short) filter, the potter can start with pre-fired clay, or grog, which is fired clay that has been ground up. Grog is normally used in ceramics as a mix-in to the clay to lend it structural strength.
The grog, or clay particles, should be sieved to two different sizes. The sizes and their ratios in the mix should vary according to the desired flow rate. If the particles are too coarse, the water flows through too quickly and if they are too fine, the water won’t flow at all.
Alternatively, the potter could use expanded shale, if shale is available. Mill the shale to size as you would the clay particles, then fire it in a rotary kiln until it pops, like popcorn, Harvey says.
Proper flow
Harvey’s experiments yielded a general formula of 60 percent coarse material to 40 percent fine. The coarse grains can be ten mesh, meaning that they can pass through a one-tenth of an inch sieve. The fine grains can be 30 mesh. That ratio gives a flow rate of about three liters per hour, Harvey says.
Then the potter treats the particles with silver nitrate and fires them. The firing temperature can be as low as 480°C, which is low enough that it can be done in small kilns in rural villages, Harvey says.
Finally, mix the differently sized particles and place them in ceramic container also treated with silver.
Ease and scale
The PPB filter may be easier to make and harder to break than candle filters, William Carty, a professor of ceramic engineering at Alfred University in Alfred, New York, wrote in his support for a grant proposal to fund PPB manufacture in Kenya.
“In my opinion,” Carty says, “the technology is robust, much easier to implement and essentially fool proof. It also has the considerable benefit of being scalable, and a well-designed packed bed water filtration system can be constructed at minimal cost and with unskilled labor.”
In the future, tests should evaluate the performance of different materials sourced locally from the communities where these are manufactured, Carty says. It is especially important to figur out how those materials affect the flow rate and the amount of time that the water is in contact with the pathogen-killing silver.
Scaling the technology may be as simple as pouring a layer of silver-treated ceramic particles in the base of a water tower or community cistern. Untreated and contaminated water could be pumped into the top of the cistern and treated water would flow out, Harvey says.
Stoves and latrines
Harvey has put ceramics to use in two other technologies for developing communities: rocket stoves and silver-treated latrine surfaces. The stoves burn fuel in a mostly closed space, reducing the fuel needed and cutting down on smoke. The treated latrine surfaces are made from packed particles and kill pathogens to limit the spread of disease.
Harvey teaches people to use the packed-particle techniques and he would like to see his designs catch on and spread, he says.
“This filter, and the other simple technologies of pottery for health, really, really should be for all,” Harvey says.
Dear Engineers for change/ rob goodier, thanks for posting the information about our granulated ceramic filters, but please checkout in addition, the following wixsite. this is largely about the other urgent of ceramics in environmental health: environmentally responsible cook stoves; self explanatory.