Medical products must be sterile to prevent the transmission of diseases. From bandages to gauze to the ubiqitous facemask, the solution to the issue of sterility hasn’t changed: make them disposable. This market is projected to grow in the next few years, with a compound annual growth rate of 16.7% from 2021 until 2028.
Although disposable medical products support global health, they also contribute to the plastic epidemic. Plastic accounts for about 30 percent of global healthcare waste. The World Health Organization estimates 87,000 tons of personal protective (PPE) equipment were produced during the first year and a half of the COVID-19 pandemic. Most of this equipment is thought to have ended up as waste.
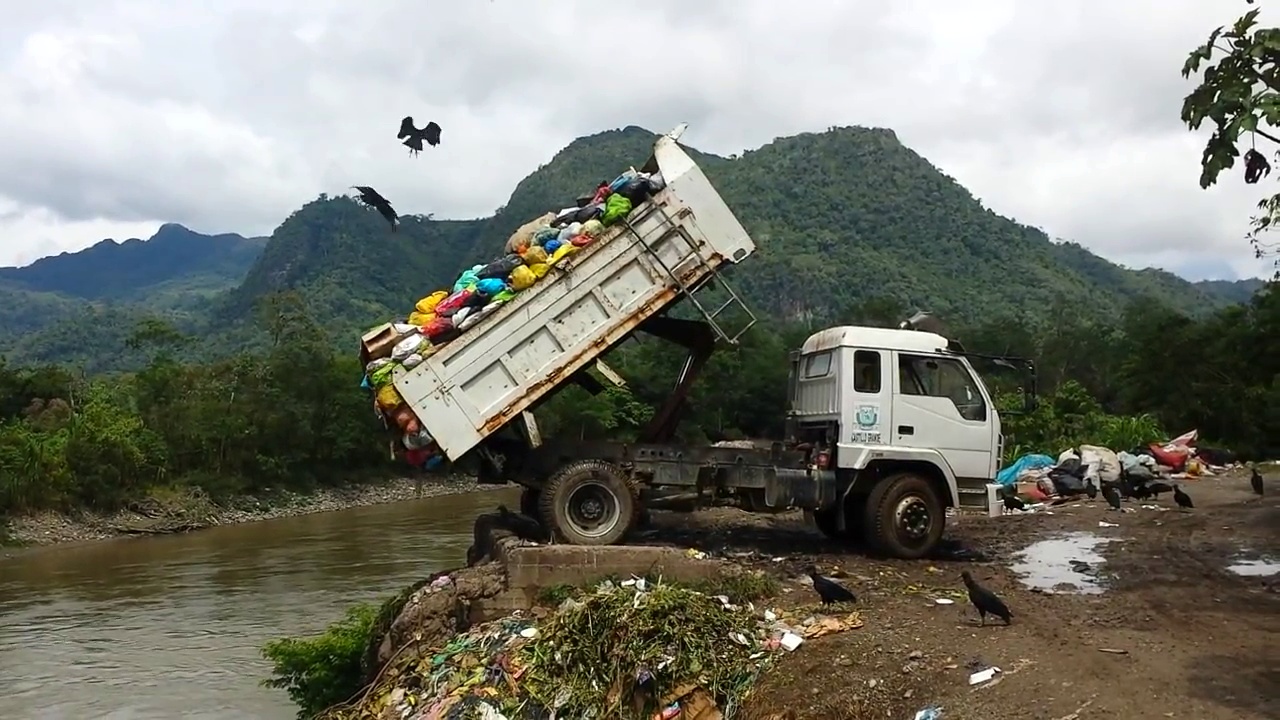
A truck dumps medical waste into Huallaga River in Peru. The dump site is less than one mile (1km) from the city of Tingo Maria. For more than 30 years trucks here have dumped 30 to 34 tons of garbage daily. Photo: Public domain
Despite efforts to bring circularity to the plastics sector, it is estimated that 75-199 million tons of plastic are floating around in our oceans.
Decomposition of these plastics will take 50-500 years to break down, and even then, it doesn’t go away – it just gets smaller and smaller, producing microplastics. Studies have shown that microplastics don’t just remain in the environment: we eat, breathe, and drink them. This is theorized to be harmful to humans, as studies have shown that they harm our cells.
We need to change our consumption habits if we want to achieve Sustainable Development Goals 3 and 12 simultaneously.
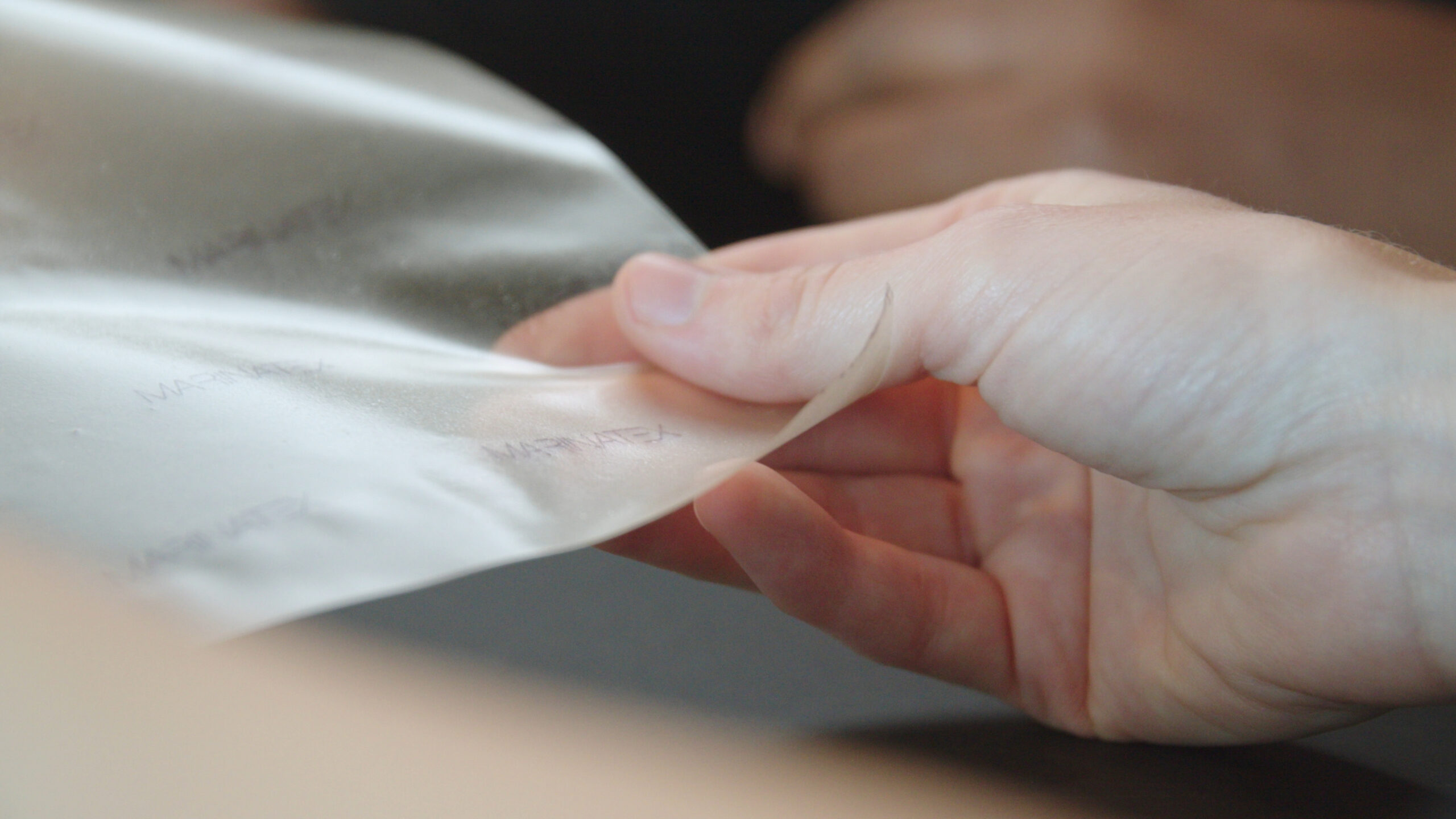
An engineer develops a biodegradable plastic. Photo: This Is Engineering (CC by NC-ND-2.0)
Thankfully, we are not powerless. There are a number of different actions we, as consumers and designers, can take to mitigate plastic waste in the healthcare center.
One such action is to buy products that use sustainable materials, such as non-plastics that will decompose over time. Sometimes these materials are even discarded from other processes, helping to spread sustainability across multiple industries. For example, straw wheat is a byproduct of harvesting wheat that is usually thrown away. SmartLifeEco uses straw wheat to produce 100% compostable dental floss picks. They even improved the functionality of the floss pick by introducing the thinnest thread on the market, helping users get to the tightest gaps without breaking the floss. Thanks to an eco-friendly lens, what was once waste is now reborn.
If plastic alternatives have been pursued but are not feasible, another option is to maximize usage. Take lateral flow kits. Thanks to the help of COVID-19, the global lateral flow test market was valued at $9 billion in 2021 and is projected to rise to $14 billion by 2030. Test kits are instrumental to decreasing the spread of COVID-19 but they also generate a lot of waste.These are disposable, non-recyclable, and if you get a negative result, you need to do another one. Of the 140 million test kits produced during the first year and a half of COVID, kits filled landfills with more than 2,600 tons of non-infectious waste, most of which is plastic. How can we mitigate this? With multiplexing.
Multiplexing rethinks how lateral flow tests are made. It refers to having more than one test on a strip or including more than one test in a cartridge. Strangely, clinical usage is less than that of research. Widespread multiplexing usage in healthcare will decrease the amount of plastic and help spurn discussions around how pursuing sustainability can have the added benefit of increasing efficiency.
Influenza A positive test result.
Test 4 respiratory infections at the same time with the combo #Fluorecare test. Available @Measie_ : https://t.co/2ZyD0KKkEF pic.twitter.com/fL8Od92ooU— Julian Brus (@BrusJulian) December 23, 2022
How about medical devices? How can we decrease their plastics consumption? One answer is leveraging technology. Rather than being subtractive, as many manufacturing methods are, 3D printing is additive so there is less waste. This has huge dividends during the prototyping process when the design is being iterated and, subsequently, various versions of the product are manufactured.
In college, my colleagues and I developed a product called MistEase, an assistive eye drop device that enabled elderly glaucoma patients to independently administer medications. We went through dozens of designs during the prototyping process, and we used a 3D printer to build each iteration. 3D printing reduced the amount of plastic that ended up in landfills by using this additive manufacturing method.
Even better, software simulations can further decrease plastic use by reducing the number of physical prototypes. Simulations can be conducted on computer-aided design (CAD) models to choose the best design before a handful, rather than hundreds, of physical prototypes are produced.
Another improvement that could be made to medical device design is accounting for the lifetime of the device. Pursue options that last longer but have minimal serving requirements. Make sure to weigh the tradeoffs with sterility requirements though, because sterilization methods can counteract the sustainability of the device. In addition, consider how components will be replaced. Do you have to replace the whole product? Or can you replace subsections to decrease waste?
The Center for Research in Simulation and Education Technologies (CREST) is doing just that with their newest trainer: the Advanced Joint Airway Management System (AJAMS). Unlike other trainers, AJAMS has easily-replaceable sections for the areas that will see the most use during procedures.
So, what can you do?
- Use your buying power to support companies that are providing sustainable options
- On the personal scale and as non-profits and governmental organizations that buy healthcare products in bulk.
- Incorporate sustainable features whenever possible during the design phase
- Increase awareness of sustainable options
- Share products with your family, friends, coworkers, etc.
Together, we can steer medical products in a new direction, one that prioritizes the health of not just humanity, but the planet too.
About the author
Elizabeth Laughlin is a former Engineering for Change Fellow who bridges the gap between mechanical engineering and technical writing across industries, including medical and aerospace. Over the years, she has discovered a passion for writing and is excited to keep learning and communicating technical subjects to audiences. Using engineering to improve the quality of life for communities around the world is urgently needed, now more than ever, and she would like to be one of the members of that initiative.