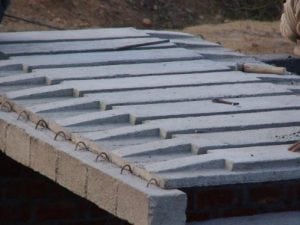
Agriculture
March 7, 2024
Precast Concrete Beams and Slabs
Read SolutionImplemented by
Technology for Tomorrow (T4T) Africa
Updated on March 1, 2024
·Created on July 18, 2017
The HyPar Thin Shell Concrete roof is a roofing system made from a mixture of cement, sand, water and acrylic latex on a mesh base forming a thin shell.
The HyPar Thin Shell Concrete Roof is a roofing system developed by George Nez and Albert Knott of [TSC Global] who trained groups in several developing countries in how to construct them. One of the groups they trained is Technology for Tomorrow (T4T) who is offering the roofs as a building product in Uganda.
The roofs are 1 cm thick and made from a mixture of cement, sand, water and acrylic latex on a fibreglass mesh or cloth and light wire mesh base. The shell layer is supported on a four-sided pyramid framework of timber that creates a hyperbolic parabola shape.
Target SDGs
SDG 11: Sustainable Cities and Communities
SDG 1: No Poverty
Target Users (Target Impact Group)
Household, Small and Medium-sized Enterprises, Public Sector Agencies, NGOs
Distributors / Implementing Organizations
TSC Global has partnered with Technology for Tomorrow (T4T), Engineering Ministries International (EMI), and the government of Haiti for their BBBC (Build Back Better Communities) campaign
Competitive Landscape
Direct competitors include Micro Concrete Roofing Tiles and Corrugated Metal Panels.
Regions
Worldwide
Manufacturing/Building Method
Made on site with materials including latex, mesh, and wood members ordered from elsewhere and brought to site.
Intellectural Property Type
Open-source
User Provision Model
Users can build the Hypar roof themselves based on published instructions (see Product Schematics section) or else hire a company that has been trained such as T4T or EMI.
Distributions to Date Status
Unknown
Unit dimensions (cm)
N/A
Primary materials
Cement
Complimentary materials
None
Fire Resistance (hr)
Unknown
Thermal Insulation Capacity
Negligible because the material is thin and high-density
Compressive Strength (MPa)
Varies based on building/roof design, mix design, and quality of construction.
Suitable Climates
Suitable for any climate but additional measures would need to be taken to insulate for colder climates
Design Specifications
The basic form is made as follows but can be adjusted to suit any building design. These specifications were taken from the book Latex Concrete Habitat by Dr. Albert Knott and Dr. George Nez. Other researchers and builders propose slight differences to the framing details and mix design, but the general process is the same.
The Edge Members: four poles with two slightly longer than the other two, and fastened so that the two longer poles meet at one corner. That corner can be lifted and propped on a post.
The Screen Surface: Posts are marked in 1' (30cm) segments and then 1' wide strips of fiberglass fly-screen are wrapped from one side of the frame to the other in both directions, layering them on so that they overlap by 6" and stapling down to the frame.
Coating and Surface: The first coat is a latex slurry mixture of latex liquid and portland cement and water and brushed on to the surface using long-handled brushes. The next layer is a latex mortar mixture made of latex slurry and sand and applied until the surface is about 1cm thick.
Other Considerations: The surface can be used for roofs, arched shelters, and walls, and additional strength provided by adding additional layers of fabric and mortar. The surface can also be perforated for smokestacks and skylights. Only hand tools are required to build the structure and electricity is not essential. It is possible to construct the roof first before the walls and the roof structure is so light that it can be lifted onto the walls afterward or can have separate columns supporting it.
Technical Support
Technical support may be provided by the trained builder of the system.
Replacement Components
The system is not modular and therefore the whole roof would have to be replaced. The materials used are available in most countries that have a construction industry and can therefore be easily obtained for any additional construction.
Lifecycle
The complete lifecycle is unknown, but there are HyPar structures that have been standing for over 20 years. Tests have shown that quality assurance is important in the construction of HyPar roofs because deterioration can happen if details or the mix is done poorly.
Manufacturer Specified Performance Parameters
Designer specified performance targets include the system being light weight, strong, durable, portable, low cost, and minimum training required.
Vetted Performance Status
Testing of the system is being performed separately and does not relate to the projects that have or are currently being completed by implementers of the system. Research has been performed for the material science of the HyPar shell to determine the optimal mix design and structural performance during an earthquake.
Safety
The roof is lightweight and would therefore not be fatal to occupants if damaged by an earthquake. Workers would be subject to general dangers of a construction site including working with sharp tools. Construction does not require the use of large machinery.
Complementary Technical Systems
T4T is pairing the roof system with ISSB walls. EMI paired the roof system with earthen bag construction.
Academic Research and References
Carlton, W. S., 2013, Material Behaviour of Latex-Modified Concrete in Thin Hyperbolic Paraboloid Shells, A Thesis Submitted to the Graduate Faculty in partial fulgent of the requirements for the Degree of Master of Science Civil Engineering.
Balding, D., 2013, The Experimental Seismic Testing of Hypar Shells, Fourth Year Undergraduate Project, St. Catharines College.
Knott, A. & Nez, G., 2005, Latex Concrete Habitat, Trafford Publishing.
Straube, J., 2011, BSD-011: Thermal Control in Buildings
Compliance with regulations
Unknown
Other Information
“Patent - Method for constructing a tensile-stress structure and resultant structures”, Google Patents, accessed on March 1, 2024, https://patents.google.com/patent/US3927496
“Rebuilding Haiti Better at the BBBC”, TSC Global, accessed on March 1, 2024, https://tscglobal.wordpress.com/
“Free Burma Rangers clinic”, Earthbag building, accessed on March 1, 2024, https://www.earthbagbuilding.com/projects/hypar.htm
Agriculture
March 7, 2024
Implemented by
Technology for Tomorrow (T4T) Africa
Agriculture
March 4, 2024
Implemented by
Lazarian World Homes
Agriculture
March 6, 2024
Agriculture
February 19, 2024
Implemented by
Earthquake Engineering Research Institute (EERI)
Agriculture
November 30, 2024
Implemented by
Sustainable Community Development Services (SCODE)
Agriculture
February 26, 2024
Implemented by
Advanced Earthen Construction Technologies (AECT)
Agriculture
February 23, 2024
Implemented by
Ital Mexicana
Agriculture
February 23, 2024
Implemented by
All Hands Volunteers (All Hands and Hearts)
Agriculture
February 23, 2024
Implemented by
Bridges to Prosperity
Agriculture
February 23, 2024
Implemented by
Habitat for Humanity
Have thoughts on how we can improve?
Give Us Feedback
I am interesting in doing this for housing in the Philippines. I understand that some of this study/research was done at OU in Norman, Oklahoma. Is it possible to visit with this person? Need a hypar that is 20 feet by 20 feet.