The caretakers of the ceramic pot water filter design are committed to supporting local manufacturing facilities and businesses, rather than outsourcing production for export and import. This is a look at the challenges of manufacturing locally around the world, and expert guidance on how to do it successfully.
Ceramic water filters look like simple flower pots – no moving parts, nothing complicated. But making them is requires the confluence of precise steps and skill. Manufacturers need to source and test the clay, adjust the ratios of materials accordingly, buy or build hardware such as a hydraulic jack press and a brick or gas kiln, develop a distribution network and manage sales. If those pieces come together, the reward is a filter manufacturer that helps to improve drinking water in nearby households. But a lot can go wrong.
The filters are manufactured by pressing a mixture of clay and burn-out material (such as sieved rice husk or sawdust) into the iconic “flower pot” shape. The pressed filters dry, then they are fired in a kiln. The burn-out material fires out in the kiln, leaving a porous matrix that filters the water. The filters are then flow-rate tested to confirm production consistency. Those that pass usually have a flow rate of 1-3 liters in the first hour from a full filter. They are coated with silver, which acts as a disinfectant. Silver is the only material in the filter that is imported and not sourced locally. The filter suspends in a standard 5-gallon bucket, water is poured into the pot-shaped membrane, then flows downward into the safe storage receptacle where treated drinking water is stored until poured from a built-in tap.
Potters for Peace has promoted this method of local manufacture throughout developing countries since 1999, providing training in set up and ongoing technical support. At last count in 2013 there were about 50 independently run facilities that have produced 700,000 filters to provide clean water for 3 million people worldwide. Those numbers are probably similar today, says Justine Rayner, a member of the Ceramics Manufacturing Working Group and the Joint Filter Committee of Potters for Peace and Potters Without Borders.
“There are many advantages to local production. It provides small business opportunity and local employment and since filters are manufactured locally there is a local supply chain for replacement parts,” Rayner says.
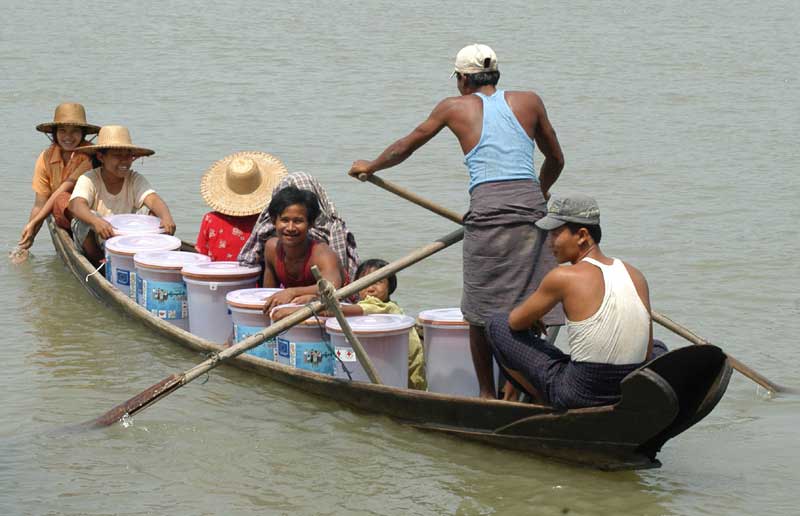
Owners of new ceramic water filters take their purchases home in Myanmar. Photo courtesy of Thirst Aid
But decentralized manufacturing can lead to uneven quality. In one example of what can go wrong, Rayner and her team at the Ceramics Manufacturing Working Group tested clay that had been sourced at a mine in Nicaragua when they found that they could not make it hold together after firing. The factory had already gone to production when Rayner’s team contacted them and they realized that they could not make filters from that clay. They had sourced a new batch of clay from a mine and had not tested it. That experience led to a valuable lesson learned, that because clay quality can vary from site to site and even in the same site, so testing a new batch is necessary before production.
Other pitfalls can open in the firing step because it is hard to get even heat distribution in a handmade brick kiln.
In 2011, the working group responded to the quality control problem with a set of factory guidelines: Best Practice Recommendations for Local Manufacturing of Ceramic Pot Filters for Household Water Treatment. And a quality control evaluation process is in development to evaluate quality control protocols and processes in factory.
One way to assess a factory’s performance is to test the filters’ flow rates.
“If there is variability in flow rates of filters from the same batch or between batches (for example, if more than 20 percent do not fall within the expected flow rate range), production is not well controlled, the filters may not work to remove bacteria as well as previously tested prototype filters, and the source of the variation should be identified and corrected,” Rayner says.
Communicating data like that, and new research such as the efficacy of silver in different kinds of water, can be tough. Communication is a big challenge in decentralized manufacture in general. The working group and the potters’ organizations send email and newsletters to the factories to update them on new research (how effective the silver coating is in hard and soft water, for example), and new guidelines. But besides the usual issues with missed email and misunderstood instructions, there are also language barriers.
Potters for Peace’s Guide to Running a Filter Factory
There is no perfect prescription for these kinds of ailments, but the potters’ organizations are gradually refining their training methods and outreach to the facilities. We asked Kaira Wagoner, Filter Project Coordinator at Potters for Peace, for tips on how to run a successful filter factory.
“Throughout our work, Potters for Peace has uncovered a few key practices that improve efficacy and sustainability of filter projects,” Wagoner says. These are
Make sure that the filter addresses the specific needs of water purification in your community before choosing it as your solution. The filter is designed to remove bacteria, protozoa and turbidity, and is not intended to address chemical or viral contamination.
Establish local ownership of filter production. The most successful filter projects are locally owned and operated. While external startup funds and support may be helpful, it is important to project sustainability that filter factories be locally owned and operated.
Identify and work with skilled potters in your community. It is often beneficial for potters to be involved in filter production, as they may have: knowledge and skills of the trade, access to raw materials and needed equipment, and access to local markets.
Work closely with one or more trained consultants during filter factory establishment. Working closely with Potters for Peace or other trained consultants can save valuable time and money. While the filter is simple to use, quality control of a health tool like the filter is extremely important, and can be difficult to establish and maintain.
Standardize production and establish strict quality control criteria. Raw materials should be carefully sourced and processed. Filter production steps including firing should be consistent and highly standardized. When possible, motorized equipment should be used for filter production. Ceramic filters should be capable of removing ≥99% of bacteria before the silver coating is added.
Develop a strong marketing plan for the filter. It is important to set aside funds for filter marketing. Market the filter as an aspirational product for all, not as a product designed for low-income households.
Do not give filters away for free. Filters are better maintained and more likely to be used correctly when people pay for them, even at a subsidized price. Exceptions can be made for schools and health clinics, especially when filter donation is used as a marketing tool.
Combine filter distribution with health and sanitation education, including information on filter maintenance. Reminding people of good health practices such as good hand-washing techniques is a powerful tool that helps reduce diarrhea incidence. Training people to use and clean the filter properly is also essential.
Provide EASY access to filter replacement parts. Filters and filter system components can break over time. It is important to establish a solid distribution chain for filters and filter system components so that when something breaks, filter users can easily access replacement parts. Local shops and health clinics can sell filters and filter system components for a small profit.
Engineers like to solve problems. If there are no problems handily available, they will create their own problems.