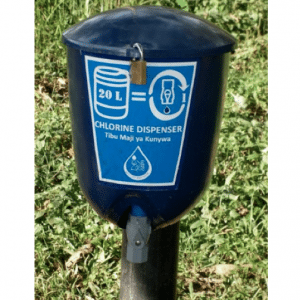
Agriculture
September 23, 2023
Dispensers for Safe Water
Read SolutionImplemented by
Innovations for Poverty Action
Updated on January 2, 2024
·Created on September 2, 2016
A flow-through system that feeds chlorine doses into passing water.
The CTI Water Chlorinator is a non-electrical water disinfectant system that was designed for communities with gravity supply water systems. The Water Chlorinator attaches to a gravity-fed water tank, delivering a controlled dosage of chlorine to a community’s water tank. The chlorine kills most disease-causing pathogens, making the water safe to drink.
Target SDGs
SDG 6: Clean Water and Sanitation
SDG 3: Good Health and Well-Being
Market Suggested Retail Price
$200.00
Target Users (Target Impact Group)
Community
Distributors / Implementing Organizations
CTI is partners with Emerging Opportunities for Sustainability (EOS) International and with Self Help International (SHI) in Nicaragua.
Competitive Landscape
Direct competitors include Lotus Water Chlorine Dosing Device and Zimba automatic chlorine dispenser.
Regions
Central America
Countries
Nicaragua
Manufacturing/Building Method
Chlorinators are manufactured locally from PVC pipe, fittings, and ¼ inch (6 mm) sheet PVC. The system is constructed with simple tools and assembled with standard PVC cement and stainless steel screws or PVC pegs. The body of the unit is a 4 inch (100 mm) PVC tee, with a 9 cm nipple and coupling on each end. A 4 inch (100 mm) riser, 30 cm long, is fitted into the branch of the tee, and is closed on top by a cap. More detail can be found in the information manual.
Intellectural Property Type
Open-source
User Provision Model
In Nicaragua, CTI and partners train villagers to install and maintain the water chlorinator. They provide sanitation education in partnership with the health ministry and identify dedicated village volunteers to replace chlorine and maintain systems. CTI maintains chlorine banks with local partners to restock systems and periodically monitor their maintenance.
Distributions to Date Status
Chlorinators have been installed in more than 600 rural communities in Nicaragua, providing safe water to more than 340,000 villagers.
Active Chemical and concentration (%)
Treatment lifespan (days)
If not stored in a covered container, 24 hours.
Design Specifications
The chlorinator must be installed on: 1) a gravity fed system, 2) where influent water with >10 ntu is filtered before passing through the chlorinator, and 3) where the flow through the chlorinator is between 2 and 10 gpm (.13 and .63 liters/sec). The chlorinator is manufactured from: 1 4? x 4? PVC T, 21? of 4? PVC pipe, 2 4? couplings, 1 4? cap, 17? of 3? pvc pipe, 1.3 square feet of 1/4? PVC sheet a small container of PVC cement and 11 #4 x 1/2? stainless steel sheet metal screws.
Technical Support
Formal water committees, called CAPS (Comite de Agua Potable y Saneamiento, or Potable Water and Sanitation Committee) are trained in operation and maintenance, including free chlorine residual testing.
Replacement Components
To keep a constant supply of chlorine tablets within short distance from local villages, CTI has established more than 20 regional chlorine banks that store small inventories of tablets for sale to local villages. These banks keep records indicating which communities are replacing their chlorine.
Lifecycle
CTI recommends estimating chlorine usage at two 140 g tablets per week. This ranges greatly depending on the water flow rate and number of operating hours.
Manufacturer Specified Performance Parameters
For an average ground water supply the maximum flow that one chlorinator can treat (including bypassed flow) is about 20 gpm (about 1.3 liters/sec).
Vetted Performance Status
CTI carried out an evaluation in Nicaragua.
Safety
Unknown
Complementary Technical Systems
Water should be stored in a safe storage container with a lid and tap to preserve water quality.
Academic Research and References
“CTI is now Bountifield International,” Bountifield International, 16-Aug-2019. Available: https://bountifield.org/cti/
EOS, “Our Model,” EOS International, 20-Jul-2016. Available: https://www.eosinternational.org/water/
“Accessing Clean Water,” Self-Help International, 21-Nov-2016. Available: https://www.selfhelpinternational.org/accessing-clean-water/
“Home,” Zimba Water, 12-Feb-2016. Available: http://zimbawater.com/
“Goal 6,” Sdgs.un.org. Available: https://sdgs.un.org/goals/goal6
Biorealis.com. Available: https://biorealis.com/OMV/files/CTI8%20InformationManual11.1-pdf.pdf
Bountifield International, “CTI-8 Water Chlorinator,” 15-Oct-2008. Available: https://www.youtube.com/watch?v=TYkP1DnOlBw
selfhelp, “Clean, Safe Drinking Water for Thousands with the CTI-8 Water Chlorinator,” 03-Aug-2015. Available: https://www.youtube.com/watch?v=SyDsqHkn1EY
Compliance with regulations
Unknown.
Evaluation methods
A study by CTI was conducted during March – June 2014 in 37 rural communities located within the departments of Matagalpa and Jinotega, and in villages with a typical, closed, gravity-fed community water system. Water samples were collected and analyzed for presence of bacteria. The study concluded that chlorination of rural water sources through the CTI-8 significantly reduces bacterial contamination of drinking water.
Other Information
Installed project video and Construction video.
Agriculture
September 23, 2023
Implemented by
Innovations for Poverty Action
Agriculture
August 4, 2024
Agriculture
January 1, 2024
Implemented by
TATA Swach
Agriculture
January 24, 2024
Implemented by
AidGear
Agriculture
January 3, 2024
Implemented by
Easol Pvt Ldt
Agriculture
December 29, 2023
Implemented by
Sawyer
Agriculture
January 24, 2024
Implemented by
Gift of Water
Agriculture
January 17, 2024
Implemented by
HACH
Agriculture
January 26, 2024
Implemented by
Warka Water
Agriculture
January 30, 2024
Implemented by
Puralytics
Have thoughts on how we can improve?
Give Us Feedback
The effort and rigor in the design and manufacturing process to secure regulatory approval should not be underestimated. This requires documentation starting at the initial design and concept stages of the product. For example, is there a documented Failure Mode and Effects Analysis to guide the design process that defines both expected and reasonably unexpected misuse of the product – and the associated design, process control and/or (lastly and least effectively) labeling to effectively mitigate these risks?
Anna Murray says:
– A reference for bacteria/virus/protozoa removal would be helpful