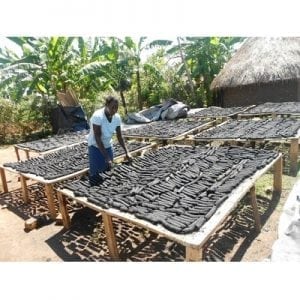
Agriculture
November 22, 2024
AEST Agricultural Waste Charcoal Briquettes
Read SolutionImplemented by
Appropriate Energy Saving Technologies Limited (AEST)
Updated on December 1, 2023
·Created on June 17, 2014
Prosthetics for the lower and the upper limbs manufactured via ICRC’s polypropylene technology.
Prosthetics for the lower and the upper limbs manufactured via ICRC’s polypropylene technology. The product was selected for inclusion in WHO’s 2013 Compendium of Innovative Health Technologies for Low-Resource Settings.
Target SDGs
SDG 3: Good Health and Well-Being
Target Users (Target Impact Group)
Household, Community
Distributors / Implementing Organizations
ICRC develops polypropylene technology and trains local professionals in the use of technology to establish local limb-fitting centers. The establishment of these local centers allows ICRC to transfer responsibility to a local government or partner NGOs. In certain circumstances, ICRC may substitute entirely for the authorities, but 90% of ICRC projects are managed in close cooperation with local partners, primarily government authorities.
Competitive Landscape
Direct competitors include Jaipur Foot.
Countries
Afghanistan, Burma, Ethiopia, Iraq
Manufacturing/Building Method
Individually crafted by a prosthetic technician on location using ICRC manufacturing guidelines.
Intellectural Property Type
Open-source
User Provision Model
Worldwide at ICRC sponsored limb-fitting centers. In 2011 ICRC-assisted centers produced 19,740 prostheses and fitted the following amount of new patients with prostheses: Africa (2,435), Asia (4,265), Europe and the Americas (393), Near and Middle East (1,527)
Distributions to Date Status
437,910 prostheses as of 2014.
Craftsmanship required
Skilled
Patient satisfaction
92%
Patient compliance
98%
Comfort
74%
Materials
Polypropylene
Water resistant (yes/no)
Yes
Amputation level
Transtibial
Weight (kg)
Unknown.
Design Specifications
The core of the prosthetic system is made of polypropylene. The injection process is used for making the components. Other parts of the prosthetic device (sockets, cosmetic covers, etc) are made of polypropylene sheets using thermoforming.
For thorough design specifications: ICRC Resource Center, Manufacturing Guidelines.
Technical Support
ICRC-assisted centers are established locally and can provide technical support.
Replacement Components
Ordered from manufacturer's website (CR Equipments Switzerland)
Lifecycle
Replace:
Adult prosthesis: 3-5 years. The child might expect to be fitted for a prosthesis 15-20 times in a lifetime.
Waste material from polypropylene technology is recycled in many countries to make components of walking aids.
Manufacturer Specified Performance Parameters
ICRC's Physical Rehabilitation Programme promotes the use of technology appropriate for the context in which it operates (primarily countries effected by war and low-income or developing countries). It lists the following guidelines for any technology it deploys for the physically disabled:
Vetted Performance Status
A study by ISPO followed 32 trans-tibial amputees using ICRC designed and manufactured polypropylene prostheses. 28 users were satisfied with the ICRC prosthesis and 23 found it to be their preferred artificial limb when compared to others. In the same study, minor failures of the prostheses were encountered, such as small cracks in the hard socket (4 instances) and cracks in the cosmetic seam (3 instances). ISPO concluded at the end of the study that ICRC's polypropylene technology can be recommended for trans-tibial prostheses. A second study by ISPO comparing ICRC polypropylene design with a conventional wood-resign design found both systems to provide acceptable technical and clinical results.
Safety
Ill-fitting prosthetic can result in physical discomfort and pain to the patient
Complementary Technical Systems
None
Academic Research and References
Jensen, J. S., Heim, S. Evaluation of polypropylene prostheses designed by the International Committee of the Red Cross for trans-tibial amputees. Prosthetics and Orthotics International. 2000 Apr; 2(1):47-54.
Jensen, J. S., Raabb, W. Clinical field testing of trans-femoral prosthetic technologies: resin-wood and ICRC polypropylene]. Prosthetics and Orthotics International. 2004; 28(2):141-151.
Compliance with regulations
Unknown, but the following standards exist for orthotics and prosthetics:
Evaluation methods
User surveys
Other Information
None
Agriculture
November 22, 2024
Implemented by
Appropriate Energy Saving Technologies Limited (AEST)
Agriculture
February 5, 2024
Implemented by
Centre for Vision in the Developing World
Agriculture
January 18, 2024
Implemented by
Agua Clara LLC
Agriculture
January 26, 2024
Implemented by
Warka Water
Agriculture
August 16, 2024
Implemented by
Guillermo Silva Pérez
Agriculture
January 27, 2024
Implemented by
Medentech Ltd
Agriculture
June 27, 2024
Implemented by
Assist International
Agriculture
March 8, 2024
Agriculture
March 8, 2024
Implemented by
Conseil Européen pour la Recherche Nucléaire (CERN)
Agriculture
June 28, 2024
Implemented by
Swoop Aero
Have thoughts on how we can improve?
Give Us Feedback